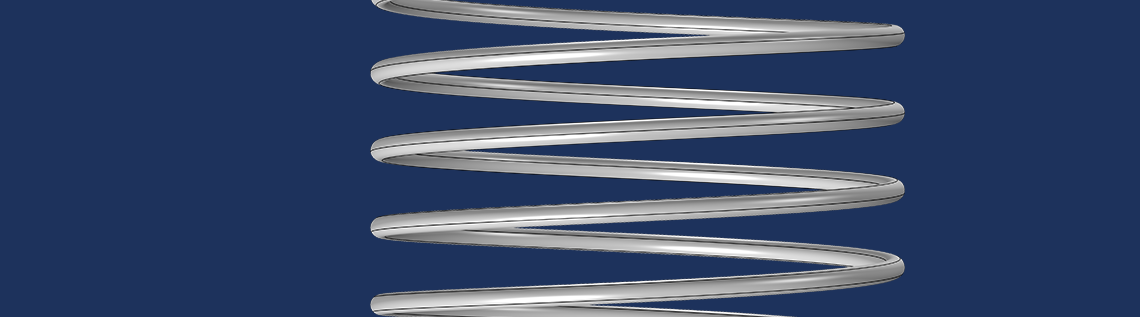
Compression springs are used in a wide range of industries, and their design can be surprisingly challenging despite their long history of use. To make the task of designing a spring more straightforward, Veryst developed a simulation app using the Application Builder in the COMSOL Multiphysics® software to provide essential design information based on rigorous finite element analysis.
Automating Helical Spring Design Using a Simulation Application
Helical springs are used in nearly every industry, from medical devices to cars and planes, from toys and consumer products to industrial products. Every engineer is familiar with the “common” helical spring — in fact, you may have had to design one during your engineering training.
An example of a helical spring.
The design of a helical spring can be complex, despite centuries of helical spring use. This design complexity derives from the intersection of spring requirements, which can include geometry limits, necessary stiffness, material selection, required longevity, and cost. In some instances, a spring that satisfies all requirements does not exist: the design problem is “over-constrained.”
Given this complexity, Veryst Engineering, a COMSOL Certified Consultant, has developed a simulation application, or app, that makes spring design tasks much easier, providing essential design information based on rigorous finite element analysis within a prepackaged app.
The Basics of the Helical Spring Design App
The Veryst app, shown below, allows a designer to input the spring geometry of the outer diameter, length, wire thickness, and number of turns. The app user can specify the material properties or select from a drop-down menu of common materials. Maximum allowable stresses can also be added to provide an approximate estimate of loading cycles to failure. The user then selects mesh density and computes the spring properties. The app calculates the response of the spring until full compression or a percentage of ultimate tensile stress, whichever occurs first.
Input interface allowing specification of the spring geometry and material properties.
Adding Complexity to the App
The app can analyze common spring geometries, including conical springs with different diameters at the spring ends. Three versions of the app were created:
- Version 1 requires the springs to be purely helical (i.e., with opened ends)
- Version 2 allows for flattened (or closed) ends, where the ends of the spring are parallel and flat
- Version 3 is a “light” version for simplified linear analysis of a purely helical spring
Example geometries are shown below. The first two versions are the same, other than the spring end types and the inclusion of self-contact needed to model closed springs. The closed-ends spring app takes approximately five times longer to run than the version with opened ends due to the added complexity of modeling self-contact within the spring coils.



Examples of permitted geometries include conical springs (with closed ends shown left, opened ends not shown); helical springs with opened ends (middle); and helical springs with closed ends (right).
Both versions 1 and 2 of the app automatically run four analyses:
- Eigenfrequency
- Linear compression
- Nonlinear compression
- Buckling
In comparison to these “standard” apps, the “light” version only performs a simplified linear analysis of the spring, which reduces computation time but restricts the number of outputs. The outputs and plots listed below are for the two standard versions.
Spring App Output
The app estimates many spring properties, including:
- Spring constant
- Spring constant based on analytical formulas for comparison
- Diametral expansion
- Spring mass
- First, second, and third natural frequencies
- Buckling load
- Maximum load
- Maximum displacement to full compression
- Maximum principal and von Mises stresses
- Analytical stress predictions for comparison
- Estimated cycles to failure based on analytical formulas
The app generates the following plots:
- First, second, and third vibrational modes
- Spring deformation
- Von Mises stress contours
- Load vs. compression curve
- Diametral expansion vs. compression curve
- Maximum von Mises stress vs. compression curve
Calculated spring properties and von Mises stress contours.
Calculated spring properties.
Watch a brief video introduction to the app on Veryst’s LinkedIn page.
The Value of an App
None of the values or plots provided by the helical spring app are particularly hard to calculate or estimate. The app, however, provides the value of a flexible and easily used — yet rigorous — finite element analysis that captures geometries not easily estimated by handbook calculations, while simultaneously providing a plethora of engineering values associated with each analyzed geometry and material. A designer’s job is, consequently, made much simpler.
Veryst Engineering develops apps for clients with difficult yet regularly needed analyses that require engineering resources that could be better used elsewhere. This helical spring app provides a simple example of how Veryst, using the capabilities of the Application Builder in COMSOL Multiphysics, can make engineering design straightforward and clear.
About the Author
Riccardo Vietri is an engineer at Veryst Engineering. Mr. Vietri holds a bachelor’s degree in mechanical engineering from Harvard University. His experience includes a wide range of mechanical testing, prototyping, modeling, simulation, and product development. His research has involved the prototyping and fabrication of a composite flight platform for a stratospheric scientific balloon experiment (SCoPeX), including modeling dynamic loading of the payload, the design of custom composite outriggers for stability during payload landing, and the construction of a variety of specialized fixtures to perform custom composite assembly testing and material characterization.
Mr. Vietri has expertise in finite element analysis, simulation, and 3D modeling using the COMSOL Multiphysics® software, ABAQUS®, and SOLIDWORKS®.
ABAQUS is a registered trademark of Dassault Systèmes Simulia Corp. SOLIDWORKS is a registered trademarks of Dassault Systèmes or its subsidiaries in the United States and/or other countries.
Comments (1)
Tuan Anh Le
January 19, 2023What Comsol module can I use for this simulation? Thanks