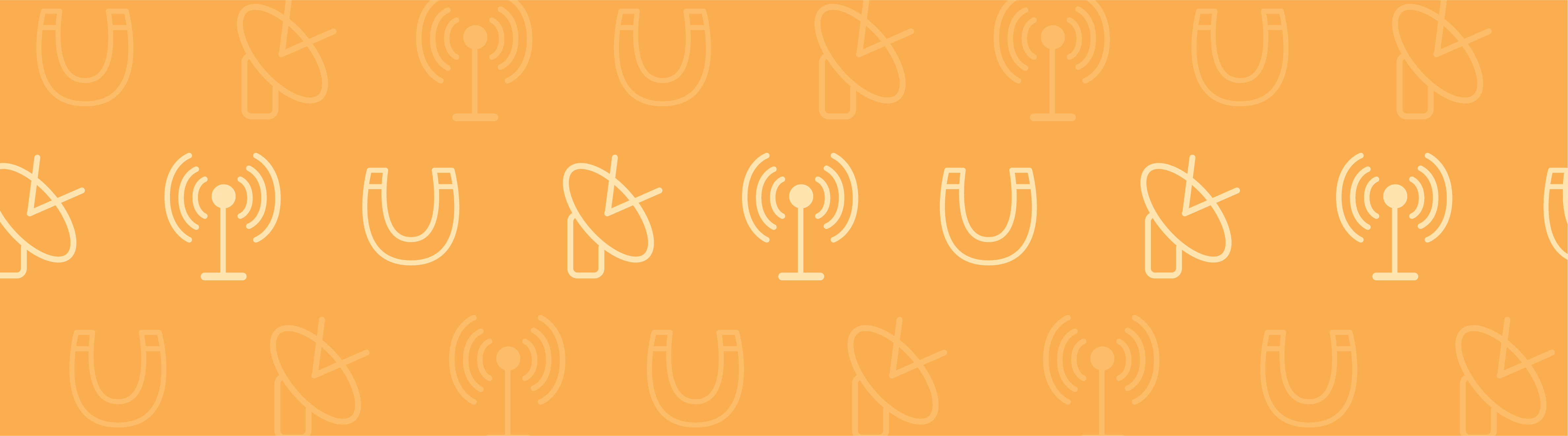
In civil engineering and the biomedical field, strain gauges are used to measure deformation sustained by various objects. Typically, foil gauges are used, but they have low sensitivity. MEMS-based gauges, like the double-ended tuning fork (DETF) strain gauge, offer better performance. To optimize the design of a new DETF strain gauge, researchers used the COMSOL Multiphysics® software and compared the results to an analytical model.
Benefits of a MEMS-Based Strain Gauge
Strain gauges measure how structures — both manmade and biological — react to an applied strain. These devices are common in the mechanical and civil engineering fields for monitoring the structural health of bridges, detecting soil pressure changes near oil drilling platforms, and testing aircraft components. Strain gauges can even be used to analyze bone structure in humans and animals.
A mechanical strain gauge used to measure the growth of cracks on the Hudson-Athens Lighthouse in New York. Image by Roy Smith. Licensed under CC BY-SA 2.5, via Wikimedia Commons.
In terms of performance, MEMS-based gauges have several advantages over standard foil strain gauges. For one, MEMS sensors have higher strain sensitivity than foil sensors, resulting in more accurate measurements. MEMS-based gauges also have higher fracture strength and can withstand high operating and bonding temperatures, which makes them more durable than their foil counterparts and expands their range of applications.
DETF strain gauges have their own set of distinct advantages:
- Small size
- High sensitivity
- High resolution
- High shock tolerance
To optimize the design of a new DETF sensor, researchers from the School of Engineering Technology at Purdue University used MEMS simulation.
Modeling a DETF Strain Gauge in COMSOL Multiphysics®
The research team created a 3D geometry of a strain gauge with the MEMS Module, an add-on to COMSOL Multiphysics. The model consists of a DETF — including the beams, base, and anchors — and an electrostatic comb drive. The researchers wanted to validate the simulation results, so they used the dimensions of an analytical model when setting up the model’s components.
The DETF strain gauge. Image courtesy A. Bardakas, H. Zhang, and D. Leon-Salas.
The research team used several of the built-in capabilities of the MEMS Module when modeling the strain gauge. The Thin-Film Damping feature was used to compute the forces between solid surfaces and the surrounding air. This effect accounts for the main cause of damping in the DETF.
The team also used the MEMS Module to set up a prestressed frequency analysis. This is important for many MEMS devices, as it helps determine the initial frequency of the device and how the frequency shifts once a load is applied.
Using a parametric sweep, the researchers determined how a range of applied forces affect the gauge without having to manually change the value and recompute the model each time. This enabled them to optimize their design more efficiently. Based on the results of the parametric sweep, the team modified the geometry to ensure that the device could accommodate a range of forces.
Evaluating the Simulation Results
The resonance frequency of the DETF gauge was computed via two methods. Using a frequency analysis, the researchers found a resonance frequency of 84.060 kHz for the model. This is slightly higher than the frequencies found using a fundamental mode analysis (83.263 and 83.271 kHz). This difference is likely because a denser mesh was used for the mode analysis.
Resonance frequency of the DETF strain gauge for different mode shapes. Image courtesy A. Bardakas, H. Zhang, and D. Leon-Salas
The team used the model to optimize the DETF strain gauge design by balancing its sensitivity and structural integrity. Next, they plan to use a two-mask silicon-on-insulator process to fabricate the design. In addition, the researchers plan to investigate strain loss in the device via further analyses and experiments.
Further Reading
- Learn more in the researchers’ full paper: “Design and Simulation of a Microelectromechanical Double-Ended Tuning Fork Strain Gauge“
- Check out other examples of simulating sensor performance:
Comments (0)