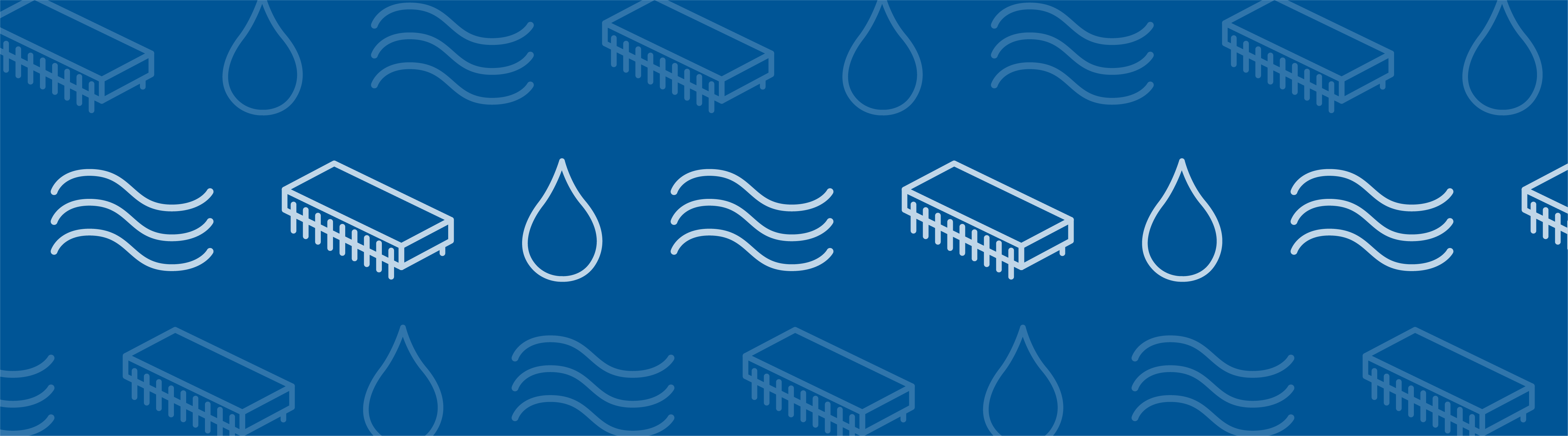
Skyscrapers, highway bridges, and other heavy manmade structures often use drilled shafts. Despite their widespread application, these shafts suffer from anomalies due to suboptimal designs and issues with the flow of concrete. To better understand such problems and improve the concreting process for drilled shafts, researchers used the COMSOL Multiphysics® software. Here, we take a peek at their preliminary research and findings.
Addressing Issues in the Drilled Shaft Design Process
Drilled shafts are deep foundation elements that are both cost effective and high performing. They can be used in a variety of soil strata with minimal noise and vibration issues. Due to these benefits, drilled shafts are used to support heavy structures around the world.
Schematic of a drilled shaft in use. Image by J. Asirvatham, A. E. Tejada-Martinez, and G. Mullins and taken from their COMSOL Conference 2017 Boston presentation.
Drilled shafts are simple structures, consisting of deep cylindrical holes drilled into soil or rock. Often, construction workers use a drilling fluid or slurry to maintain the hole’s stability during the excavation process. They do so by pumping an amount of slurry that is equal to the removed soil into the excavated hole.
When the hole reaches a required depth, a reinforced steel (rebar) cage is added. The excavation hole is then filled with concrete via a long pump truck hose or tremie. This device pumps the concrete into the bottom of the hole, preventing it from mixing with the slurry.
The main stages of the drilled shaft creation process: Drilling the excavation hole (left), inserting the rebar cage (middle), and filling the hole with concrete (right). Images by J. Asirvatham, A. E. Tejada-Martinez, and G. Mullins and taken from their COMSOL Conference 2017 Boston presentation.
In an ideal situation, concrete effortlessly displaces the lighter slurry as it fills the excavation hole. However, this is not always the case in reality. Different rebar cage shapes and placements change how concrete rises as well as generate head differentials between the concrete inside and outside the cage. The kinematics of the concrete flowing into the excavation hole can also cause anomalies. For instance, a poor flow of concrete from the tremie can produce a drilled shaft that is lower quality across the entire cross section and depth.
Left: Comparison of an idealized concrete flow to an actual concrete flow in situations involving a drilling fluid or slurry. Right: An anomaly caused by poor concrete flow performance. Images by J. Asirvatham, A. E. Tejada-Martinez, and G. Mullins and taken from their COMSOL Conference 2017 Boston paper and presentation, respectively.
When performing experimental tests to investigate these issues, a research team from the Department of Civil and Environmental Engineering at the University of South Florida noted that the flow pattern of concrete into drilled shaft excavation holes has a large influence on the properties of the hardened cast of the drilled shaft. In addition, they saw that the placement of the reinforced steel cage could cause anomalies in the form of creases.
To achieve a concrete flow that properly fills a drilled shaft hole, the research team decided to simulate the drilled shaft concreting process. We take a look at this work below.
Analyzing the Concreting Process for Drilled Shafts with COMSOL Multiphysics®
For their study, the team created a preliminary 2D axisymmetric drilled shaft model consisting of a rectangular element that is 7 feet deep with a 4-foot diameter. At the center of the model is a tremie pipe with a 10-inch diameter. Surrounding this pipe are rebars, which take the shape of vertical elements with gaps. The model can account for the rheological properties of the concrete, the potential structural blockages, and the two-phase flow of:
- Concrete flowing from the tremie pipe
- Slurry being displaced by the concrete and flowing out of the excavation hole
The researchers used a level set method, included in a two-phase flow interface in COMSOL Multiphysics, to compute the motion of the interface between the concrete and slurry.
Drilled shaft model geometry. Image by J. Asirvatham, A. E. Tejada-Martinez, and G. Mullins and taken from their COMSOL Conference 2017 Boston paper.
With this model, the team simulated the flow patterns and volume fraction of concrete and slurry over a 4-minute time period. They also calculated the head differential between the inside and outside of the rebar cage.
At the beginning of the time period, the concrete (depicted as red in the plots below) remains within the tremie, while the slurry (depicted as blue) fills the rest of the excavation hole. As time progresses, concrete begins to flow out of the tremie and move vertically up within the rebar cage. After developing the required head, the concrete starts to flow radially out of the rebar cage and spreads into the annular space. This continues as concrete fills more and more of the excavation hole, displacing the slurry. However, the concrete does not fill the space evenly, resulting in a head differential between the inside and outside of the rebar cage.
Non-Newtonian simulation results, showing the volume fraction of the concrete (red) and slurry (blue) at different times. Images by J. Asirvatham, A. E. Tejada-Martinez, and G. Mullins and taken from their COMSOL Conference 2017 Boston paper.
The non-Newtonian simulations calculate a head differential of 0.35 meters (14 inches), which is within the observed experimental range of 0.20 to 0.40 meters (8 to 16 inches). On the other hand, the Newtonian simulations show a difference of 0.90 meters (36 inches), which is higher than the observed range. Thus, the non-Newtonian flow model is more appropriate for this concrete flow simulation and demonstrates that simulation can successfully calculate the concrete head differential in a drilled shaft.
The researchers used their preliminary simulation results to predict how the concrete flow velocity and rebar spacing affect the concrete head differential between the inside and outside of the rebar cage. Here, the researchers found that the differential increases as the concrete velocity rises and when the clear spacing of the rebar is reduced.
Next Steps
The initial 2D axisymmetric model results are promising because the calculated flow patterns are consistent with the observations from the project site. In the future, the researchers want to examine how this process is influenced by the size of the drilled shaft and the design of the rebars. They plan on expanding their model to 3D to further study the concreting process.
These models can help to determine the ideal rheological properties and optimized workability of fresh concrete so that it can better fill a drilled shaft with a given size and rebar arrangement.
Learn More About Using Simulation for Civil Engineering
- Check out the full paper: Numerical Modeling of Concrete Flow in Drilled Shaft Construction
- Read these related blog posts:
Comments (4)
Sayed-Abbas Kazemi
December 17, 2017Is it possible to share the mph file?
raoudha sassi
April 11, 2018Is it possible to share the mph file?
Caty Fairclough
April 12, 2018Hi Sayed-Abbas and Raoudha,
Thank you both for your comments.
While this specific model file is not available for download, we encourage you to browse our Application Gallery for tutorial examples: https://www.comsol.com/models.
raoudha sassi
June 5, 2018Hi Caty
Thak you for answering me
but I just need what boundary conditions are used to provoke the concrete flow