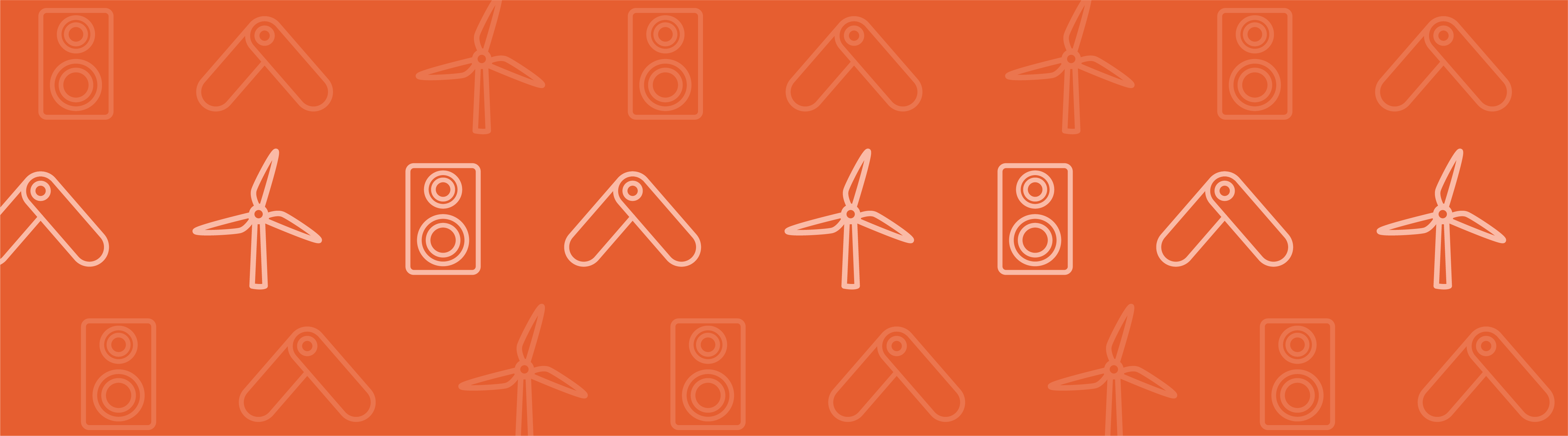
Imagine a mode of air travel that is both fuel efficient and environmentally friendly. The mechanical modeling of torque transfer components in fully superconducting rotating machines have helped researchers draw new conclusions on how to optimize aircraft design and potentially achieve electric propulsion. A research team investigated the stress and heat distribution in these machines and presented their results at the COMSOL Conference 2013 in Boston.
Balancing Structural and Thermal Needs
With the use of COMSOL Multiphysics, Tingcheng Wu, Guillaume Escamez, Clement Lorin, and Philippe J. Mason from the Department of Mechanical Engineering at the University of Houston were able to perform simulations to analyze how individual components of the structure impacted its overall performance. By applying various parameters to the structural design, they were able to conclude which factors had the greatest effect on the machine, both structurally and thermally. Thus, they could determine how to achieve a balance between the two.
Optimizing Torque Transfer Components
The team of researchers modeled the structure as a rotor shaft separated into five individual parts connected by bolts. As a means to provide thermal insulation, different materials were used on particular areas of the shaft, as you can see below.
Bolts were used to connect stainless steel with G10, a glass fiber material characterized by low thermal conductivity and a high yield stress. Image by T. Wu, G. Escamez, C. Lorin, and P. Mason, and taken from their poster submission.
Seeking to analyze the issues of heat transfer and solid mechanics in these machines, the researchers used the Heat Transfer Module and Structural Mechanics Module to create their simulations. The figure below highlights the team’s findings regarding temperature, depicting that the G10 components take on the greatest temperature gradient.
In the next figure, the connection bolts underwent the most stress within the structure, a factor that was found to decrease as the cross-section area was decreased.
Simulations highlight the thermal and structural pressure that the shaft endured, especially along its connection bolts. Image by T. Wu, G. Escamez, C. Lorin, and P. Mason, and taken from their presentation.
The Future of Fully Superconducting Rotating Machines
With the continued funding and efforts of NASA and other research teams, progress continues to be made in the design of aircraft. As torque transfer components within fully superconducting rotating machines continue to be optimized, researchers gain momentum in their quest for developing structures with greater power densities and the potential for electric propulsion. In addition to making air travel a quieter and more energy efficient process, implementing this technology paves the way for its potential use within modes of ground transportation as well.
Download the Research
- Access the paper, presentation, and poster: “FEA Mechanical Modeling of Torque Transfer Components for Fully Superconducting Rotating Machines“
Comments (0)