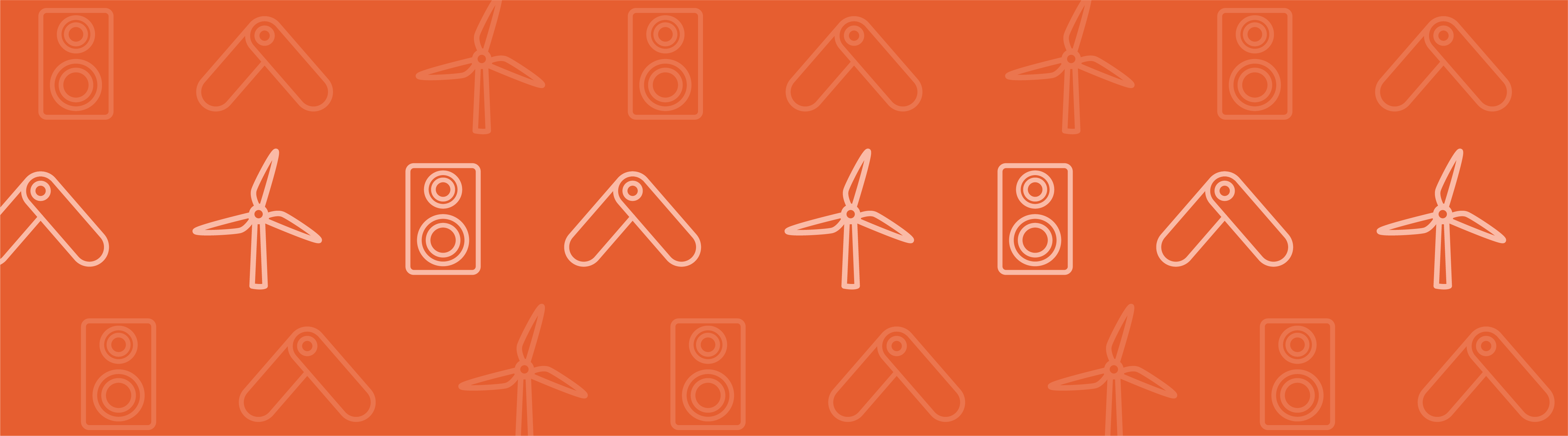
For gas pipeline maintenance standards, the adage “rules are meant to be broken” may not apply, but “rules are meant to be updated” certainly does. Specifically, the generous distance requirements between pipeline squeeze-off locations and pipe fittings cause potentially unnecessary digging. This prompted Operations Technology Development (OTD), a partnership of natural gas distribution companies, to initiate a project with Gas Technology Institute (GTI), where researchers used simulation to investigate the standard distance requirements for streamlined and safe pipeline maintenance.
Squeeze-Off: A Key Procedure in Gas Pipeline Maintenance
Squeeze-off is a procedure used for gas pipeline maintenance and repair. The process involves compressing a pipe to completely stop the flow of gas with a squeeze-off mechanism. Squeeze-off must be performed slowly to avoid damaging the pipes.
A diagram (background) and photo (inset) of a general pipe squeeze-off procedure.
The American Society for Testing and Materials (ASTM) has set standards for the squeeze-off procedure for gas pipelines. The location of the squeeze-off tool from the nearest pipe fitting must be either three lengths of the pipe diameter long or about 30 cm (twelve inches) long, whichever distance is greater.
This creates problems in the pipeline maintenance industry, as most average consumer pipes have a diameter of about 6 cm (2.375 inches). Although three lengths of this common pipe diameter is about 18 cm (seven inches), the standards say that the squeeze-off distance must be whichever length is greater, meaning that the squeeze-off tool would still have to be placed about 30 cm away from the pipe fitting. This can lead to digging into main roads and detours, causing costly and inefficient maintenance procedures.
These ASTM standards prompted researchers at GTI, sponsored by OTD, to investigate a question: Is the 30-centimeter distance for squeeze-off locations really necessary for smaller pipes, or can the standards be updated to allow smaller pipes to use the three-pipe-length diameter?
Analyzing Stress and Strain in Pipes with COMSOL Multiphysics
The team at GTI, Oren Lever and Ernest Lever, researched their question by implementing a fully parametric, time-dependent model of a polyethylene (PE) pipeline with a squeeze-off and fitting. They used both the Structural Mechanics and Nonlinear Structural Materials modules in COMSOL Multiphysics to define the numerical and mechanical properties of two sets of structural contacts: internal pipe-to-pipe contact and external pipe-to-squeeze-off contact.
The simulation enabled the researchers to analyze large deformations in the pipe at each of the different stages of the squeeze-off process, which include:
- Pressurization of the pipe
- Squeeze-off
- Hold
- Release
- Relaxation
A simulation of the five steps of the squeeze-off process.
The total displacement of the pipe when it is fully squeezed off.
The team also meshed the pipe under the squeeze bars of the squeeze-off mechanism to analyze the very large deformations that occur when the pipe is fully squeezed off and the gas flow is completely shut down. With the meshing capabilities of the COMSOL software, this process could be easily scaled to different pipe sizes besides the common 6-centimeter-diameter pipe.
Implementing a Customized Material Model
The polyethylene material that makes up the pipe in question exhibits unique properties and behaviors, which the researchers needed to capture by way of a customized viscoelastic-plastic constitutive model. For this, they turned to Veryst Engineering, a COMSOL Certified Consultant, for assistance with implementing the chosen material model into their COMSOL Multiphysics simulation.
First, the team at Veryst chose the experimental material tests that were needed to calibrate the material model typically used for polyethylene, a thermoplastic. Then, they fit the parameters of this material model to the stress-strain response of the polyethylene material. Finally, they implemented a set of ordinary differential equations (ODEs) needed to use the customized material model in the simulation.
For the material tests, GTI used a medium-density polyethylene (MDPE) pipe material. They tested it in tension and compression at different temperatures; strains; and strain rates, especially at high levels of strain (such as when the pipe is completely shut off). They also performed loading and unloading tests on the chosen material.
Tensile response of the MDPE material from experimental data and custom material model implemented by Veryst Engineering.
They then used their own MCalibration optimization tool to find actual values of material parameters that fit the experimental data, ensuring that the custom material model was a very good fit for GTI’s simulation.
Analyzing the Results and Taking Action
Through their research, GTI found that for smaller pipe diameters, such as those smaller than about 9 cm (3.5 inches), the closer squeeze-off distance of three pipe diameters would not cause strains that went beyond the current strain limits accepted in the pipeline industry.
To further validate their results, the researchers used accelerated lifetime testing. They found that under their updated standard squeeze-off distance, pipes would have an 80-year lifetime at an average operation temperature of 20ºC. This is actually the current industry-accepted standard life expectancy for these pipes.
Results from the accelerated lifetime testing for the polyethylene pipe.
With their question answered through simulation and testing, GTI is now helping to revamp standard gas pipeline maintenance procedures to be more efficient and cost effective, without sacrificing the most important element: safety.
Further Reading
- Read the full story about GTI and gas pipeline maintenance on page 18 of COMSOL News 2016
- Browse the COMSOL Blog for more information on simulation applications involving nonlinear structural materials
- Explore the latest functionality and tools for nonlinear structural mechanics modeling in COMSOL Multiphysics® version 5.2a
Comments (1)
Steve Steve
February 28, 2024Efficient gas pipeline installation requires meticulous planning, skilled labor, and quality materials. Prioritize safety, adhere to regulations, conduct thorough site assessments, and employ advanced welding techniques. Regular inspections ensure longevity and reliability. Engage experienced professionals for a seamless, durable, and compliant installation.