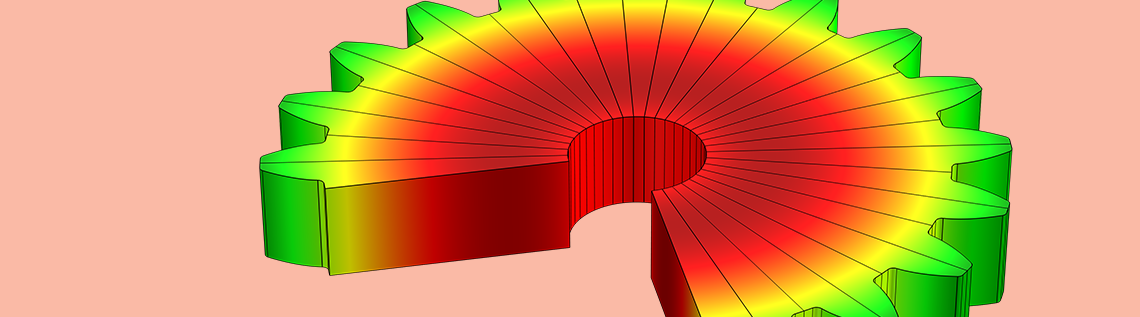
The release of COMSOL Multiphysics® version 5.5 includes the Metal Processing Module for studying heat treatment processes like quenching and carburizing. The module includes features and functionality to model phase transformations and related phenomena in materials like steel and cast iron. It can be combined with the Structural Mechanics and Heat Transfer modules to enable the computation of residual stresses and deformations in components during heat treatment. Get to know the Metal Processing Module in this blog post.
What Are Phase Transformations?
When an iron alloy like steel is heated above a certain temperature, it transforms into gamma-phase iron, also known as austenite. In a carbon steel, this metallurgical phase exists above a temperature of about 730°C, where the material is still in a solid state. On cooling, the austenite decomposes into phases of different crystal structure, and importantly, different mechanical properties. The exact mixture of phases, or the phase composition, will depend on the rate of cooling and on the chemical composition of the alloy. If the rate of cooling is sufficiently high, very hard martensite will form, and at lower cooling rates, softer phases like ferrite and pearlite may form.
During the manufacture of steel components, heating and cooling are used in a controlled manner to attain desired mechanical properties. For example, in the automotive industry, components like axles, gears, crankshafts, and camshafts are heat treated to obtain a hard and durable surface, while maintaining a relatively soft interior. A far older application of heat treatment can be found in swordsmithing. The Japanese katana is an example where great care goes into the quenching process. The idea is to produce a sword with a sharp and hard edge, and a resilient spine. It is accomplished by insulating all but the edge during quenching to limit the cooling rate of the interior, which produces a hard martensitic edge and a soft pearlitic interior — a process called differential quenching.
17th-century Japanese katanas, with their characteristic curved shape and single-edged blade (Historical Museum of Bern). Image by Rama — Own work. Licensed under CC BY-SA 2.0 FR, via Wikimedia Commons.
Metal Processing Module Overview
The Metal Processing Module brings two new physics interfaces, Metal Phase Transformation and Austenite Decomposition, for analyzing metallurgical phase transformations. Both of these interfaces provide functionality to model diffusive as well as displacive phase transformations.
The module provides more sophisticated heat transfer functionality when combined with the Heat Transfer Module, with the ability to compute effective thermal material properties as well as phase transformation latent heat and the effects of heat radiation. Similarly, by combining it with the Structural Mechanics Module and its add-on modules, you can compute residual stresses, phase transformation strains, and deformations. The Metal Processing Module interfaces can also compute effective mechanical material properties and phenomena like transformation-induced plasticity (TRIP), and thermal strains can be included.
The Metal Phase Transformation Interface
The Metal Phase Transformation interface is used to study metallurgical phase transformations that occur in a material like steel during heating or cooling. The interface provides two features: Metallurgical phase and Phase transformation.
The Metallurgical phase feature is used to define:
- The initial phase fraction
- Material properties for the phase
The Phase transformation feature is used to define:
- A source phase
- A destination phase
- Input data and settings that define how the destination phase forms at the expense of the source phase
Three types of phase transformation models are provided in the Phase transformation feature:
- The Leblond–Devaux model
- The Johnson–Mehl–Avrami–Kolmogorov (JMAK) model
- The Koistinen–Marburger model
The first two models are suitable for diffusion–controlled phase transformations, such as when austenite decomposes into ferrite. The last model is suitable to model the displacive (diffusionless) martensitic phase transformation. In addition to these models, you can define your own phase transformation models. The intuitive user interface in COMSOL Multiphysics® lets you define the phases and phase transformations in your model. The figure below shows example settings for a Phase transformation feature. It uses the diffusion-based Leblond–Devaux model to describe how Metallurgical Phase 1 transforms into Metallurgical Phase 2. Here, the input data consists of the temperature-dependent functions func1 and func2.
Settings for a phase transformation that uses the Leblond–Devaux model, with Metallurgical Phase 1 and Metallurgical Phase 2 as the source and destination phases.
When the Metal Phase Transformation interface is added, two Metallurgical phase nodes and one Phase transformation node are automatically generated. This is the minimum requirement to set up such a model. You can then define an arbitrary number of additional phases and phase transformations in your model.
The Austenite Decomposition Interface
The Austenite Decomposition interface is based on the Metal Phase Transformation interface, but specialized to simulate the quenching of steels. When this interface is added, the Metallurgical Phase and Phase Transformation Model Builder tree nodes that represent the most common phase transformations during austenite decomposition are automatically generated.
Multiphysics Functionality
In many practical situations, phase transformations induce residual stresses and deformations. For example, a steel component that is being quenched will experience the highest cooling rates on the surface, while the interior will cool more slowly. This inhomogeneous cooling is important because it gives rise to an inhomogeneous distribution of stresses and phase transformation strains.
The Metal Processing Module provides two multiphysics coupling nodes to facilitate coupling to the Heat Transfer in Solids and Solid Mechanics interfaces. The Phase Transformation Latent Heat multiphysics coupling is used to include heat released or absorbed during metallurgical phase transformations. The Phase Transformation Strain multiphysics coupling is used to include TRIP, plasticity of the individual metallurgical phases, and thermal strains.
The multiphysics couplings can be used with both the Metal Phase Transformation and Austenite Decomposition interfaces. In addition, the Metal Processing Module interfaces can compute effective mechanical material properties, and these can be used transparently by Heat Transfer in Solids, Solid Mechanics, as well as other interfaces in your model.
Computation of phase transformations, coupled to heat transfer and solid mechanics.
Steel Quenching Example
When you use the functionality presented above, you can, for example, perform steel quenching simulations of transmission components. As an example, let’s consider the carburization and subsequent quenching of a steel gear.
During carburization, carbon diffuses into the surface of the gear, and this affects the onset of martensitic transformation. Quenching in oil is simulated, and the final phase composition, residual stresses, and distortions are computed. It is shown that high residual compressive stresses appear at the root of the gear. To try this example yourself, see the Carburization and Quenching of a Steel Gear model.
Carburization and quenching of a steel gear: Computed carbon content (left) and residual stress (right).
Other Applications of the Metal Processing Module
The functionality provided by the Metal Processing Module is not limited to iron-based alloys like steels and cast irons. For example, the titanium-based \alpha – \beta dual phase alloy Ti-6Al-4V, frequently used in additive manufacturing, displays phase transformations that can be modeled using the Metal Phase Transformation interface. The possibility to implement an arbitrary number of phases and diffusive and/or displacive phase transformations is suitable to model the dissolution and formation of \alpha and \beta phases in the material.
Another application for the Metal Processing Module is the detailed analysis of the heat-affected zone (HAZ) during welding. It is well known that the base material near the melt pool is affected by the heat from the welding process, and that phase transformations will give rise to distortions and residual stresses in the weld.
Next Step
Find out more about the dedicated functionality for modeling metallurgical phase transformations in the Metal Processing Module by clicking the button below:
Comments (0)