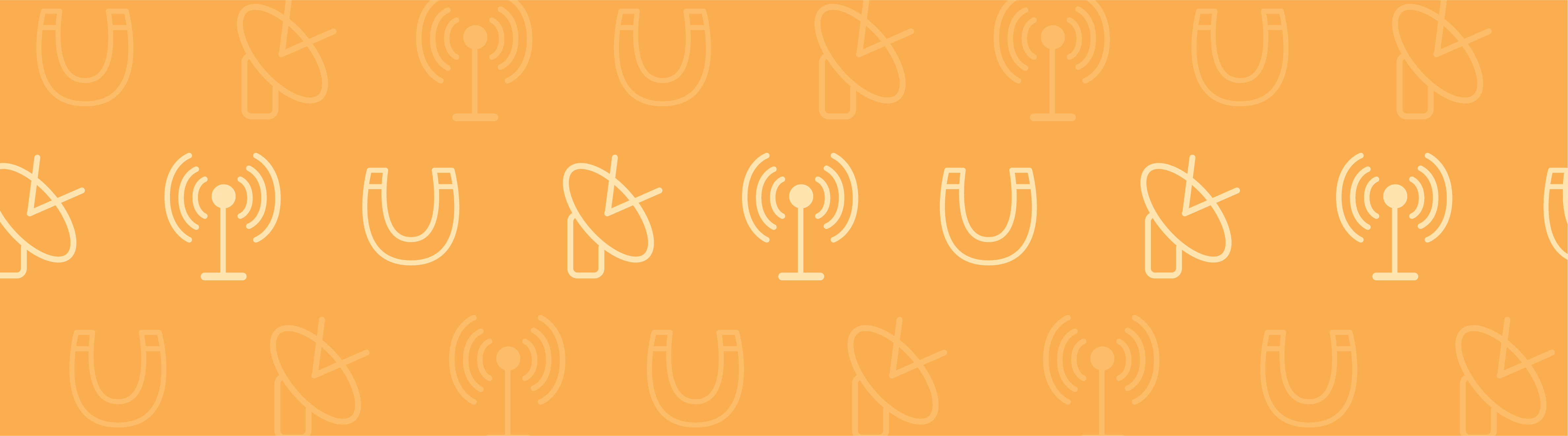
Our day-to-day lives are dependent on the safety of technical systems and processes. We blindly trust that reactor vessels withstand the test of time, that the train or ship we’re on does not break down. These metal structures, in turn, rely on accurate welding processes. Here’s where BAM Federal Institute for Materials Research and Testing comes into the picture. BAM researchers have been working on improving upon the high-power laser beam welding process in order to promote safer and more reliable metal structures – with the help of magnets.
What is High-Power Laser Beam Welding
As you can infer from its name, laser beam welding is a particular welding technique that leverages lasers for precision welding to combine multiple metal parts. The precision stems from the concentrated heat source of the laser beam; a fraction of metal in the beam’s path vaporizes, creating a vertical cavity called a keyhole. The keyhole is created by way of the dissipating vapor that puts pressure on the molten metal, causing it to become partially displaced. The material simultaneously continues to melt, thus surrounding the keyhole by molten metal. As the process continues through the workpiece, the molten metal that flows around the keyhole solidifies along the way, creating a deep and narrow weld, with a uniform internal structure.
The Challenges with Laser Beam Welding of Aluminum
Now that we’ve covered the basics of why laser beam welding is beneficial, let’s discuss its challenges when it comes to aluminum. Aluminum has a low viscosity, generating high-dynamic melt. This brings forth certain challenges with the laser beam welding process. In short, considerably wide weld pools are caused by the highly dynamic behavior in concert with the high heat conductivity. When this happens, the weld surface’s stability is compromised, leading to spattering and ejected droplets from the weld metal. This, in turn, results in craters, blowholes, blowouts, underfills, or undercuts. The bad news here is that this can lead to a subpar metal component with missing material. In that case, the metal must be post-treated (to fill in the missing material, or simply improve it from an aesthetic stand-point) with arc welding.
Those droplets I mentioned also make the welding process “dirty” when they move off of the weld bead. The Marangoni effect that is at work further complicates the weld process by being a surface effect making the liquid metal flow velocity and temperature distributions non-uniform, and potentially causing stresses and/or distortion of the piece. The non-uniformity is brought on by the fact that the weld pool is moving under electromagnetic forces and surface tension, and that the bead solidifies at different rates in different parts.
Wine Glass Shape Bad, Homogeneous Shape Good
All is not lost, however. The effects I just described may be counteracted. Researchers from BAM, located in Berlin, Germany, are looking into counteracting the Marangoni effects by using magnets. With the use of COMSOL Multiphysics, they have figured out what magnetic field distribution is needed in order to improve the weld’s uniformity by reducing the impact the Marangoni effect has on the weld. Through simulations, the researchers noted that when you do not apply a magnetic field to the weld its shape resembles a wine glass. Once a magnetic field is applied, however, the shape is more homogeneous — looking more like the letter “V”.
![]() |
![]() |
Plot of the temperature in the symmetry section of a weld shows that without any magnetic field applied (left), the weld takes on a wine glass shape. With the addition of a magnetic field of 2 T, the shape starts to take on the form of a V (right).
To cross-reference their simulation results with actual welds, they cut and polished macrosections of welds with and without magnets, and then superimposed the simulation results onto images of the actual welds. As you can see, they match closely:
A photo of actual welds with COMSOL Multiphysics results superimposed over them. The left image shows a weld without any applied magnetic field and the resulting wine glass shape. The right image shows the case with a magnetic field of 0.5 T and how the weld has a V shape.
At this point, BAM knows how to improve the welding process, and their next step is to put it into practice.
Get the Full Story
Interested in seeing how BAM conducted their research? You can read this article on page 30 in COMSOL News 2013.
Comments (0)