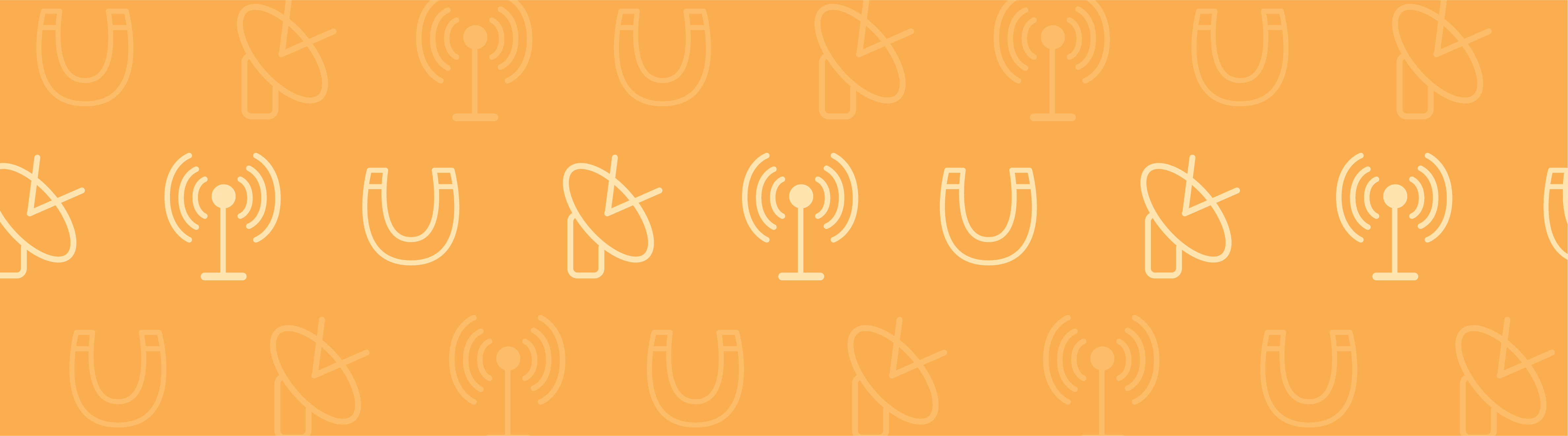
Today we welcome another guest post from Kyle Koppenhoefer of AltaSim Technologies, a COMSOL Certified Consultant. In this entry he will discuss modeling MEMS energy harvesting devices.
During our recent webinar with COMSOL on thermal-structure interaction modeling, we at AltaSim Technologies demonstrated modeling of a MEMS energy harvester that scavenges waste heat. Examples of sources for waste heat range from microprocessor chips, to internal combustion engines, to chemical processing plants. If the waste heat generated from these cases could be used to generate additional energy, then overall energy consumption could be reduced. Estimates from CANMET Energy Technology Centre indicate that worldwide, waste heat exceeds 1 TJ annually.
Maximizing Energy per Cycle of a MEMS Energy Harvester
The device modeled in the webinar consists of bimetallic cantilevered beam subjected to a thermal cycle. The beam tip contacts a hot surface and heat conducts into the bimetallic beam. As the beam heats up, the difference in coefficient of thermal expansion between the two metals generates a bending moment that causes the beam to deflect. Once the beam has lost contact with the heating surface, the beam begins to cool and return to the undeformed shape. The beam will eventually contact the heating surface and continue the deformation cycle. This bimetallic strip can be used with a range of materials that convert mechanical energy to electrical current, including piezoelectric, pyroelectric, and ferroelectric materials. Applying these materials to the bimetallic strip produces electrical energy with each mechanical cycle. Maximizing the energy per cycle then becomes the design goal.
Notes from the Thermal-Structure Interaction Webinar
COMSOL Multiphysics provides the modeling environment needed to consider each aspect of the design. During the webinar, we demonstrated how to develop a model of the heat transfer and mechanical deformation of the MEMS energy harvesting device. The model included both mechanical and thermal contact. The thermal contact released in COMSOL 4.3b represents a key feature for modeling the device accurately. As the mechanical force increases between the cantilever and hot surface during cooling, the heat transfer becomes more efficient. The coupling of the mechanical and thermal contact within COMSOL Multiphysics provides the most accurate solution of this design.
If you missed the webinar, you can catch a clip about modeling the MEMS energy harvester in the Video Center.
Modeling of the conversion between mechanical and electrical energy was not demonstrated in the webinar since the focus was on thermo-mechanical analysis. COMSOL Multiphysics provides the ability to model piezoelectric, pyroelectric, and ferroelectric materials. With the addition of these physics, the model would provide a direct calculation of the device efficiency for converting waste heat to electricity.
About the Guest Author
Kyle C. Koppenhoefer, Ph.D., has 20+ years of experience working with computational analysis. Together with Jeffrey Crompton, he started AltaSim Technologies, LLC eleven years ago to assist in new product design through the application of advanced computational tools. To facilitate this goal, AltaSim Technologies became a founding member of the COMSOL Certified Consulting program, and continues to be a leader in providing COMSOL services to those interested in receiving the benefits of modeling with COMSOL Multiphysics. In addition to guest blogging for COMSOL, AltaSim Technologies also blogs about multiphysics modeling on their own website.
Comments (1)
pedram sarmadi
November 10, 2015Hi. I have a similar project. I want to produce electricity from heat energy by pyroelectric materials but I cant find the module that includes this substance. can you help me? thanks