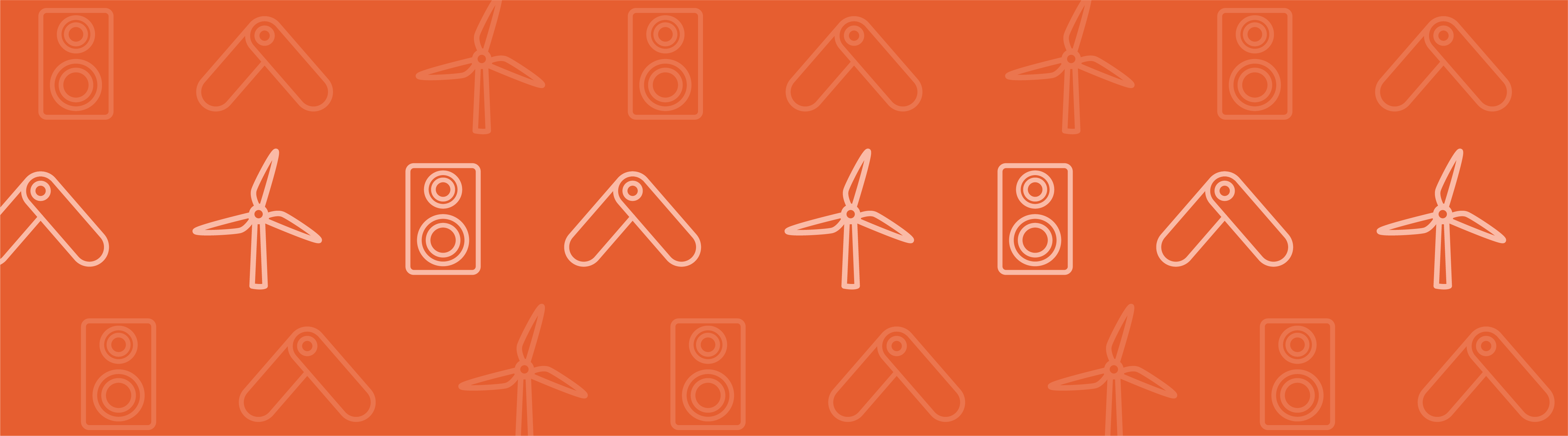
SOund NAvigation Ranging, or Sonar, has been an important part of naval warfare and since the 1950’s. Although it is a relatively simple way to locate objects, it’s the best for doing so in water, emitting sound waves and listening for echoes made by objects in the water. In today’s world of undersea warfare, the threats and the necessary responses to them are becoming more important and urgent. Sonar systems are required to detect these threats, making it necessary for researchers to increase performance as well as reduce the weight, size, and cost.
The Naval Undersea Warfare Center Division in Newport, RI develops and evaluates technology for submarines, autonomous underwater systems, and undersea weapon systems. Stephen Butler, an Acoustical Engineer and Principal Investigator, used COMSOL Multiphysics to speed up the development of a new type of sonar acoustic projector. Knowing that simulation is more accurate, faster, and more cost-efficient than trial-and-error experimentation, Butler developed the directional “dogbone” (Class VII) transducer using COMSOL’s Acoustics Module. The “dogbone” is effective because it generates highly directional beams from a single element instead of from an array of elements, thus reducing diffraction, size, and weight.
Conventional Class IV flextensional transducer and the new Class VII “dogbone” directional flextensional transducer.
The Acoustics Module was used because it includes structural, acoustics, and piezoelectric elements. These multiphysics couplings helped Butler derive appropriate AC drive coefficients, allowing the acoustic pressure output to double in one direction, and be nulled in the other direction. This was a multistep process, which began with validating the accuracy of the simulation software. After sufficient comparison between experimental and modeled results, more detailed simulations were performed. Without the coupled-acoustic modeling capability, it would not have been possible to derive the drive coefficients, necessary to design the “dogbone” transducer.
For a more in-depth analysis of the modeling involved in creating the “dogbone” flextensional transducer, go to page 18 in COMSOL News 2012 Magazine.
Comments (0)