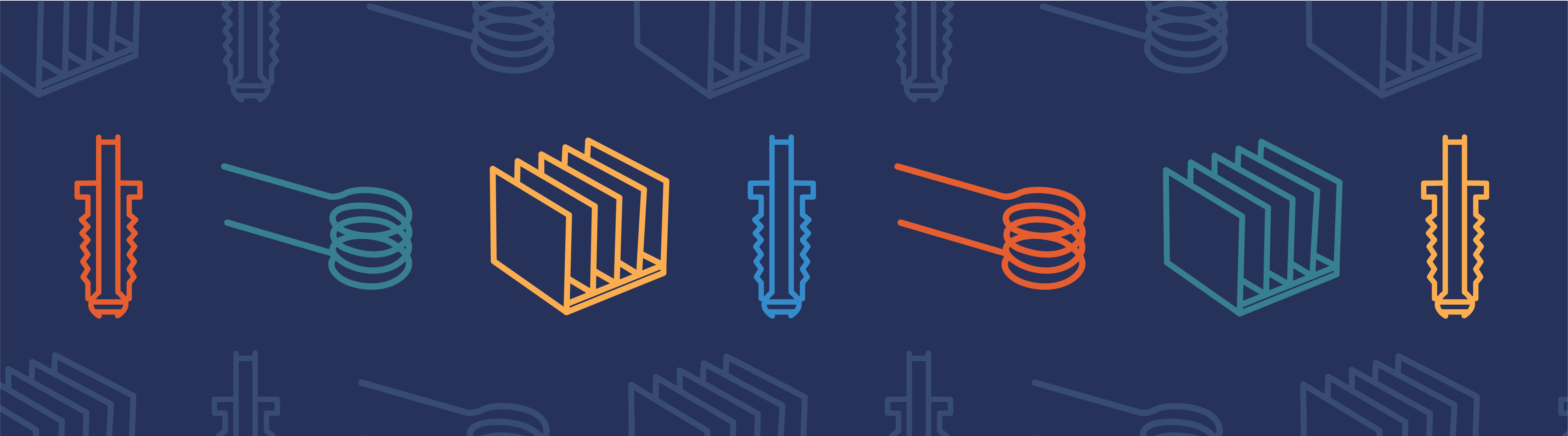
The most streamlined way to find solutions for your design parameters is to use parameter optimization with the LiveLink™ products. This is helpful when you know what results you want, but you don’t know the optimal parameter values that lead to them.
Faster Solutions with Parameter Optimization
When solving a problem of this kind, the simplest (and least effective) method is to pick a value and solve to see how close you were (a sort of “guess-and-check” method), adjust accordingly, and repeat…. and repeat… and… you get the idea. Running a simulation multiple times to find one solution is decidedly not an effective way of modeling.
A great feature of COMSOL Multiphysics is the parametric sweep, which allows you to solve for multiple parameters at once. However, you are still using the guess-and-check method, just with multiple guesses per check. Why not let the computer do the work for you?
With the Optimization Module, an add-on to COMSOL Multiphysics, you can set the desired result and the unknown parameter(s) that are involved. The software will then solve for the parameter value(s) that lead to that result, within a tolerance of your choosing.
Optimizing a Tuning Fork
Suppose we are tasked with creating a tuning fork that sounds the note A, i.e., a frequency of 440 Hz. For that frequency, we would arrive at a tuning fork prong length of 7.8 centimeters based on an existing theoretical estimation. However, when we run the model using that length, the eigenfrequency actually turns out to be 430 Hz, which is a pretty significant difference. This error occurs because the estimation assumes the prongs to be cantilever beams, when in reality, that is not the case. Uh-oh.
Wait a minute, all is not lost. We can use that as an initial value to run an optimization study. By setting the resulting frequency to be exactly 440 Hz, the resulting length of the prongs turns out to be 7.96 centimeters. For this model, we used the Nelder-Mead optimization method. There are three other methods that can be used for geometric parameter optimization: Coordinate search, Monte Carlo, and BOBYQA.
A surface plot showing the displacement and a table showing the optimized length of the fork’s prongs at 440 Hz.
Seamless Geometry Transfer with the LiveLink™ Interfaces
COMSOL Multiphysics performed many iterations to find a result within the given input tolerances (seen in the table below). With the LiveLink™ Interfaces, the CAD program and COMSOL Multiphysics work side-by-side, synchronizing the geometry after each step. Each time the length parameter (LL_d1) is updated in COMSOL Multiphysics, it is also updated in your associated CAD program. That way, once the geometry is optimized in COMSOL Multiphysics, it is also updated in your CAD program, eliminating the need to transfer your results manually.
The 19 iterations solved to arrive at the final result.
Model Download
You can download and build the model yourself. Here are the different versions of the model (note that you must also have the Optimization Module):
Comments (0)