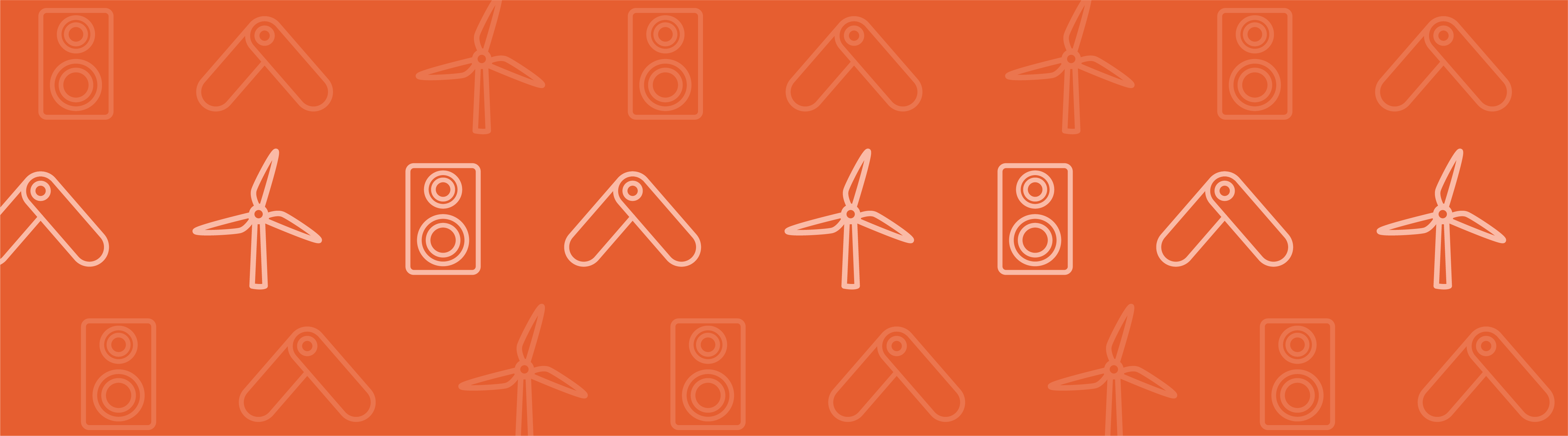
It’s not always obvious what a major role temperature control plays in modern technology, as the interchange happens in the background. Plate heat exchangers, made up of successions of metal plates and various coiled pipes, regulate and manipulate temperature, and they get the job done quickly — thanks to an active surface that is large with respect to their volume.
Plate Heat Exchangers Are All Around
As summer rolls in, your use of air conditioning and refrigeration is bound to ramp up, at home and at work. As it does, heat exchangers are involved in the process. When you take a dip in a swimming pool you will notice if the water is the right temperature or not, and your level of comfort is directly influenced by the plate heat exchanger that controls the water temperature. Apart from leisure activities, fluid temperature control also plays a key role in food safety, keeping liquids chilled or sterilized. There are many heat exchange devices out there, but what gives plate heat exchangers a leg up on other ones is the fact that they are smaller, more compact, and easier to build. It is possible to install both the condensing and the vaporizing sections in order to save space, weight, and installation costs. This is especially important for instances where there is not a lot of room to install devices, making them the perfect option for tight spaces and construction plans with time constraints.
An interchangeable plate heat exchanger, image courtesy of Varem S.p.a.
Simulating a MEMS Plate Heat Exchanger
In the micro-world, where space is an expensive commodity, a MEMS plate heat exchanger works with these same basic principles. Here, you want to exchange as much heat as possible, in as small a volume as possible, and thus maximize the contact between the exchanging fluids. A sinusoidal pattern to the plates separating the fluids helps with this maximization.
You can simulate this type of plate heat exchanger in COMSOL Multiphysics, and users have done just that with the Heat Transfer Module. The model shows a design that is built from stacked pleated sheets with a small gap between them. Cool fluid flows between the corrugated walls, while warming fluid circulates through the gaps. In the model, only the cross section of a representative geometry is considered between two sinusoidal plates, as show below, in order to investigate the fluid properties:
A section of plate heat exchanger geometry.
The medium that the MEMS plate heat exhanger relies on is plain water, and the operating temperature can be anywhere from 25°C to 80°C. The viscosity and heat capacity change significantly as functions of the temperature. A laminar inflow boundary condition with an average velocity of 15 mm/s and a temperature of 25°C is specified at the inlet. The corrugated walls have no-slip conditions for the velocity field and a fixed temperature of 80°C.
Along the length of the heat exchanger, there is a great variation in temperature, as the below image illustrates:
When determining how effective a plate heat exchanger is, pressure drop, the overall heat transfer coefficient, and mixing-cup temperature should all be considered, as well as the significance that either conduction or convection plays on the heat transfer. With COMSOL Multiphysics, the tools are available to try out many potential designs and fluids, and with simulation you can really optimize them.
Model Download
- Heat Transfer: Plate Heat Exchanger model
Comments (2)
Jigar Parekh
July 1, 2013Hello,
I have done project on CFD analysis of Plate Heat Exchanger using Fluent.
My chevron angle was 30 degress (with vertical).
>> What is the chevron angle in the above mentioned study?
>> Was this model optimized for oxide-based nanofluids as a coolant ?
Laura Bowen
July 18, 2013Hello Jigar Parekh,
Thank you for your questions. Please find my responses below:
1. What is the chevron angle in the above mentioned study?:
As the plate temperature is fixed (80°C) at the corrugated walls in the cross section represented above, the chevron angle does not affect the result for this cross section representation of the heat exchanger.
2. Was this model optimized for oxide-based nanofluids as a coolant?:
In the results shown above, pure water has been used as a coolant. However, loading material properties of a nanofluid in the model and solving it again is all you need to simulate the behavior of the heat exchanger with enhanced thermal properties of the coolant and to account for reologic properties (for example different temperature dependency of its viscosity).