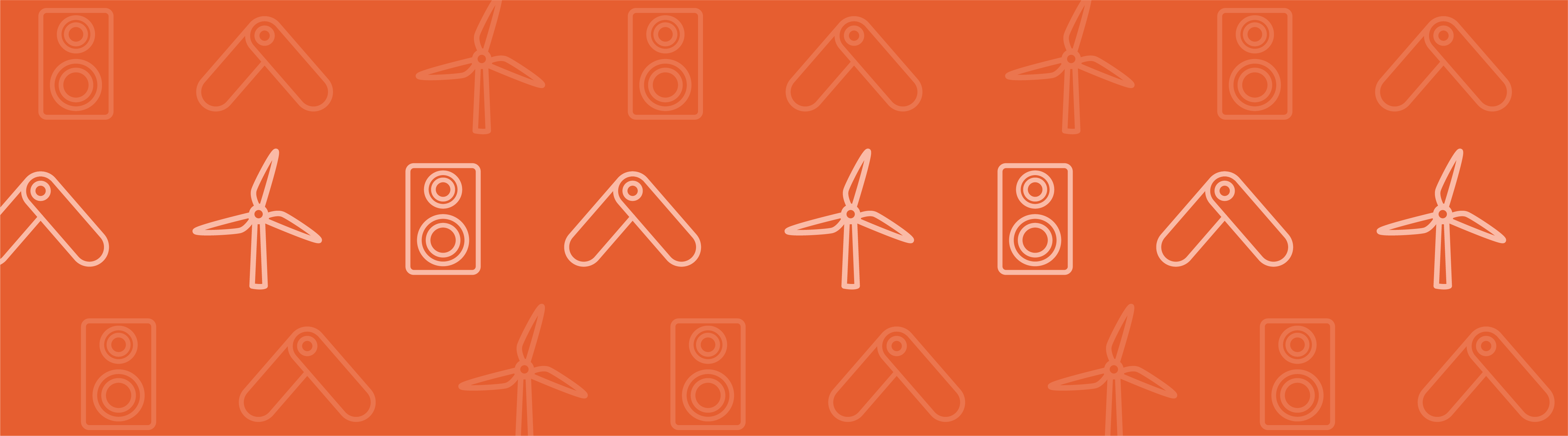
Computer aided engineering (CAE) helps us understand how mechanical systems work before they are physically realized. In order to properly reflect the reality, we continuously increase the modeling complexity when we simulate, validate, or optimize our applications. A simple technique to improve a model is to increase the number of finite elements that in turn create more evaluation points. The hardware and simulation time, however, may limit the size of the model, and other solutions are necessary — such as submodeling, for example.
The Concept of Submodeling
Many times, in numerical simulations we need to model a large structure in order to properly prescribe the boundary conditions. However, the critical part may be local and occupy only a small region of the model. In those cases the submodeling technique can prove useful.
In submodeling, you first analyze the behavior of the entire model. The mesh is chosen so that the boundary conditions and loads are properly transferred to the entire model. In other words, the field variables, displacements, and temperature should give proper results globally, but the derivatives, such as strains, may not be accurate locally.
In the second step, you cut the critical part out from the global model. The cut should be sufficiently far from the critical point so that the results of the global model give a good representation. An example of how a wheel rim can be submodeled is shown in the figure below. The red rectangle in the global model to the left denotes the part that is reanalyzed in a submodel and the purple color in the submodel to the right denotes the interfaces that cut the global model.
A full model and a submodel of a wheel rim.
The results from the global model are prescribed to the submodel by specifying boundary conditions with field variables that are applied on the cutting interfaces. In COMSOL Multiphysics, this is done using the general extrusion operator, which can transfer results from one geometry to another. Since the submodel is a small part of the full model, it can be modeled with a finer mesh, offering a better resolution of the critical part. In the final step, the submodel is resolved for the same load cases as the global model. It is of course possible to have several submodels within the same global model.
Structural Analysis of a Wheel Rim
Several CAD programs can be used to generate geometries that can then be imported into COMSOL with the CAD Import Module or one of the LiveLink™ products for CAD. This approach is powerful when you are analyzing a complex geometry. A good example of a complex geometry is the wheel rim model in our Model Gallery. This model contains many details, and a numerical representation requires many elements in order to properly resolve the stress gradients at the multiple fillets. With the submodeling technique, the local effects can be captured in such a complex model.
First you would run an analysis of the full model. Since not all details are meshed with a fine mesh, locally the results have low accuracy, at least in terms of stresses. In most of the wheel rim, however, the geometry is fairly smooth and the results are satisfactory. From the analysis of the full model, the highest stress is found at a fillet on the back of the wheel rim between a spoke and the hub where the wheel is attached to the vehicle. This critical part is further analyzed in a submodel. The submodel is cut out from the global model by taking a block that encapsulates the critical point and that has boundaries far from the critical point where the displacements from global model have good accuracy. The solution from the global model is prescribed on the cut boundaries, and the submodel is solved using a fine mesh in the critical fillet.
Comparison between von Mises stresses in a global model and a submodel. The global model underestimates stresses with about 20%.
The wheel rim model also demonstrates how to reduce solution time when analyzing periodic models. The rim can be divided into five periodic cells where each cell has a spoke pair. When the wheel rolls, the load propagates around the wheel. This periodicity in the geometry and the load is utilized in the submodeling. In the global model, only 1/5 of the whole load history is simulated. This means that spoke pair One experiences a load that moves between its center and the spoke pair immediately following, while spoke pair Two experiences a load that moves between the first preceding spoke pair and its own center. Spoke pair Three, on the other hand, experiences a load that moves from the second preceding spoke pair until the first preceding spoke pair. This is utilized by prescribing the results of the global model to the submodel via a double loop.
In the first instance, the analysis is looped over the spoke pair number, while in the second instance, the analysis is looped over the load case. For each spoke pair number, the expression in the general extrusion is changed so that results from the correct spoke pair is prescribed as boundary conditions on the submodel. This is easily done by prescribing a pure rotation:
where is the spoke pair number,
and
are the displacements, and subscripts
and
denote the submodel and the global model.
In essence, this means that the whole load cycle in the submodel can be obtained by picking results from different spokes, since they experience different loading conditions.
Thermal Fatigue in Microelectronic Components
Microelectronic components consist of several parts, such as printed circuit board (PCB), solder joints, resistors, and chips, for example. Solder joints connect the chips with the PCB and have a twofold function. On one hand, they hold the chip in place and on the other, they create a connection for the electric current. Very few materials have satisfactory structural, thermal, and electrical properties and their material models are highly nonlinear. They deform elastically together with creep or plasticity. One challenge when modeling with nonlinear materials is the increased analysis time. In addition to that, several iterations are needed; separate equations must be solved for the additional degrees of freedom (DOF), representing the inelastic strain at each integration point. In the case of a 3D model, 7 extra DOFs are used in addition to the 3 displacement DOFs of the elastic analysis. Moreover, if you are dealing with a multiphysics application where, besides the structural study, you also need to include a thermal or an electrical analysis in the simulation, additional DOFs are introduced.
In the model of thermal fatigue in viscoplastic solder joints, which is available with step-by-step instructions in our Model Gallery, two chips are connected to a PCB with several solder joints. When the power is switched on, the chips generate heat that spreads to the rest of the model and flows to the surroundings. Since the power is continuously switched on and off, a concern arises whether or not the chips will fail due to thermal fatigue. This application is simulated using the submodeling technique since a good resolution of the solder joints would give an extremely large model.
First, we run a coupled thermo-mechanical analysis on the full model. The thermal results have good accuracy also when modeled with a coarse mesh, since we only need the temperature field, and not its derivatives. The initial structural analysis will not give enough accuracy at the solder joints, especially at the interface between the joint and the surrounding material. The choice of a coarse mesh will give low accuracy of the stresses, and the viscoplastic law has a nonlinear dependency on the stresses. Using the coarse mesh in the solder joints, they are evaluated from the fatigue point of view in order to identify the critical solder ball. The Darveaux model (an energy-based model) is used to predict the fatigue life. The accuracy in the fatigue life prediction is not sufficient for quantitative conclusions to be drawn, but the results can be used for identification of the critical spot and improved on in a second submodeling step.
Fatigue life of viscoplastic solder joints. Red color represents short fatigue life and blue long fatigue life. The critical solder joint is located below the larger chip in the corner of the ball grid array. All four corner joints have approximately the same life.
Once the critical solder joint is identified, a submodel is created. The submodel contains the critical solder joint and parts of the chip and the PCB. Structural results from the global model are prescribed via a general extrusion operator onto the submodel boundaries where the cut was made in the full geometry. The thermal results are directly prescribed to the entire model via the thermal expansion and are also used in the nonlinear material model. This can be done since the thermal results of the global model have sufficient accuracy. In such a way, the initial multiphysics analysis is reduced into a single physics analysis. Finally, we solve the submodel using a fine mesh giving accurate results for both stresses and fatigue life in the critical component.
Comparison of meshes for the global model and the submodel. The global model consists of 300,000 DOFs while the submodel of a single solder ball consists of 100,000 DOFs.
Submodeling Examples
I’d like to share two examples of submodeling with you.They require different products and are therefore found in different modules.
- The Submodel in a Wheel Rim model, found in the Model Library of the Structural Mechanics Module
- The Submodeling of Thermal Fatigue in a Ball Grid Array model, found in the Model Library of the Fatigue Module and also requires the Nonlinear Structural Materials Module
Comments (3)
Shashank Tiwari
June 19, 2018Hello:
I am trying to carry out submodeling using “General Extrusion” operator. I was wondering if it is necessary to cut the the critical part out from the global model to perform submodeling?
I am working on a problem in which the global model has only three domains. My submodel is a cylinder (one of the domains in the global model). I created this cylinder in the submodel (not cut out from the global model) (with same dimensions and material properties as in the global model) and used “General extrusion operator” to transfer results from global model to submodel.
I was wondering if this approach is correct as I did not “cut” this cylinder from the global model?
While defining the “General Extrusion operator”, I was wondering if I need to select all the three domains of the global model as the source or should I only select the cylinder as the source as I did not performed any cut in the global model?
I look forward to hearing your comments.
Thanks,
Shashank
Henrik Sönnerlind
June 20, 2018 COMSOL EmployeeHi Shashank,
There are no limitations on how you create the geometry for the submodel. It is independent of the global model.
As for the definition of the extrusion operator, it does not really matter whether you select only the cylinder, or all three domains. As long as the submodel boundaries fit in the extrusion selection (there is also a tolerance), it will work as expected.
Regards,
Henrik
Shashank Tiwari
June 20, 2018Hi Henrik:
Thank you very much for your response. It is a great help.
Shashank