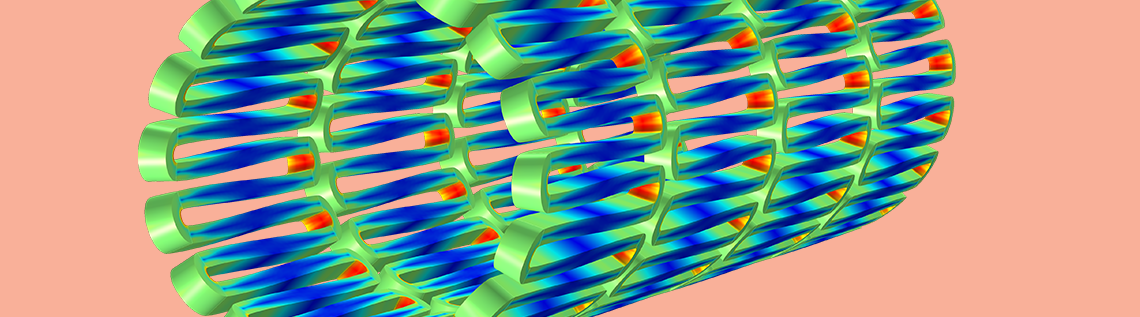
Shape memory alloys (SMAs) are alloys with “memory”: They can return to their original shape after being deformed via a change in pressure or temperature. SMAs are used in a wide variety of applications — including metallurgy, manufacturing, biomedicine, and children’s arts and crafts — and their uses are always expanding…
What Is a Shape Memory Alloy?
A shape memory alloy is a material that undergoes a phase transformation when it experiences a mechanical stress or temperature change. When the conditions return to normal, the SMA “remembers” its original shape and reverts to it.
Watch the video for a closer look at shape memory behavior!
The two crystal structures of SMA materials are known as austenite and martensite. Austenite is the SMA’s structure at higher temperatures, while martensite is the structure at lower temperatures. The transformation from austenite to martensite or vice versa is the cause of this “memory” behavior.
The basic phase transformation process in an SMA.
Common materials for SMAs include copper-aluminum-nickel and nickel-titanium alloys. The latter is often referred to as nitinol, which refers to its elemental makeup (ni for nickel and ti for titanium) as well as where it was first discovered (nol for Naval Ordnance Laboratory, which we will discuss later in this blog post).
A coil made out of a nickel-titanium alloy, an SMA.
If you search “nitinol” on various ecommerce sites, it is not hard to find SMA wires and other types of memory materials available for purchase.
The Accidental Discovery of Shape Memory Alloys
The discovery of the unique behavior of SMAs is a story in itself. Early research into SMAs took place in the 1930s, when scientists looked into certain unexpected behaviors exhibited by different metals. Swedish chemist Arne Ölander noticed and described a pseudoelastic behavior when observing a gold-cadmium alloy. However, the term “shape memory alloy” did not come into play until a laboratory accident happened around 30 years later…
In the late 1950s and early 1960s, the U.S. Naval Ordnance Laboratory was working on metallurgy research, as described in Ref. 1. A scientist named William J. Buehler was melting and casting bars of nickel titanium. While waiting for the bars to cool, he dropped one of the cooled bars on the concrete floor and noticed that it caused a dull thudding sound. He found this odd and dropped a bar that was still hot, which produced a lighter sound, like a bell. Worried that something had gone wrong in the casting process, Buehler ran to a drinking fountain and cooled the hot nickel-titanium bar under the water. When he dropped the now-cool bar, it produced the thudding sound.
A happy accident: Dropping a nitinol bar on the floor led to the discovery of its unique memory behavior.
The effect was later demonstrated in a Naval Ordnance Laboratory meeting. Buehler’s assistant passed around a thin strip of nickel-titanium alloy that had been stretched, bent, and folded like an accordion. When the object reached Dr. David S. Muzzey, he took out his pipe lighter and heated it. The alloy quickly unfolded and reverted back to the original thin strip shape. After realizing the unique qualities and behaviors of the nickel-titanium alloy under different temperature conditions, the material came to be known as nitinol, an SMA.
More recently, and looking to the future, the development of shape memory materials has moved beyond alloys. Shape memory polymers, and other variations of shape memory materials, have been developed and even released for different commercial uses.
Manufacturing SMAs for Applications Across Industries
The unique behavior of SMAs makes them an attractive choice of material for manufacturing products and components in a wide range of industries. (Ref. 2)
Aerospace
In the aerospace industry, SMAs are used to develop lightweight, quiet, and efficient designs: three factors that are always a point of focus for aircraft. Components such as variable area fan nozzles, vibration dampers, and actuators are created with SMA materials. These devices are austenitic at their normal temperature and then transform to martensitic (and the desired shape) when cooled via temperature change due to airflow around the aircraft or even the ambient temperature change that occurs during a normal flight.
The change in temperature used to induce the phase change can be brought about in different ways. There can be an electronic component that heats the SMA device, or the temperature change can be caused by excess air from the aircraft’s other parts.
A sample of a shape memory material being used in aircraft research and development. Image by Science Museum London/Science and Society Picture Library. Licensed under CC BY-SA 2.0, via Wikimedia Commons.
A more recent technological advancement for shape memory materials in aircraft is wing morphing. SMAs are being used to develop an adaptable aircraft wing that can bend and change shape while in flight.
Automotive
Back on the ground, automotive vehicles also benefit from SMAs, although the reasons have more to do with comfort and ease of use than operation. For example, some cars include an SMA valve for the pneumatic bladders in the seats. At a certain pressure, the lumbar support in a seat contours to the driver or passenger.
SMAs have also been used to build actuators that make vehicle trunks easier to close as well as noise, vibration, and harshness (NVH) valves to control noise and vibration in engines (an important performance indicator in the automotive industry).
Buildings
Building design is another application area in which SMAs are useful. Including SMA rods in concrete beams, for example, can help prestress a bridge or building. On a smaller scale, shape memory materials can be used for reliable pipe fittings in a pipe network.
Medicine
The use of SMAs for biomedical applications can reduce the need for medical intervention in patients. For example, medical stents can be implanted in arteries as a minimally invasive way to improve blood flow in cardiac patients. Microactuators and artificial muscles rely on SMAs for robotic prosthetics, which helps give patients with amputated limbs more freedom of motion.
Stents, a minimally invasive cardiac treatment method, are commonly made out of SMAs. (Note: This image, taken from the Plastic Deformation During the Expansion of a Biomedical Stent tutorial model, does not include SMAs and is purely meant to illustrate the application discussed above.)
On a smaller scale, SMAs are also used in orthodontia, such as braces; and optometry, such as glasses. If glasses frames are made with a shape memory material, they don’t have to be replaced if they get bent out of shape. Instead, they can be heated and return to their original shape.
Other Uses of SMAs
Recently, shape memory materials have been applied to consumer electronics. For instance, autofocus components for smartphone cameras as well as certain mobile antennas can be made out of SMAs.
Certain craft projects and toys also use SMAs. One example is “bendy bracelets”, which are made with a shape memory material that enables them to bend and twist before easily returning to their original bracelet shape. (The Slinky® toy, unfortunately, is made out of a type of steel and won’t return to a tightly wound coil after getting tangled — a common struggle of children everywhere.)
Drawbacks and Design Considerations
When developing a design or component made out of an SMA, there are certain factors and risks to consider. A major drawback of SMAs is the risk of fatigue failure. There are only so many times certain SMAs can be bent and deformed before they return to a shape that’s a bit different from the original one (or they break).
Another drawback is the considerable lag time of the phase change for certain SMAs. If you search for “shape memory alloy” videos online, you can see that the time for the material to return to its original shape can be slow and unpredictable.
Drawbacks such as lag time and fatigue can cause issues during the phase transformation cycle for SMAs.
From a manufacturing standpoint, SMAs can be expensive to produce, which limits their accessibility to manufacturers and consumers. Also, since most of these materials rely on temperature to undergo changes, it could be risky to use SMAs as part of a device that operates under uncontrolled or unstable temperature conditions. An SMA used for an automotive application, for instance, must be able to perform under all possible temperature conditions that a vehicle might experience.
Modeling Shape Memory Alloys in COMSOL Multiphysics®
The mechanics of an SMA are difficult to describe because of the complexity of the phase transformations that take place. This complexity can make modeling SMAs quite the endeavor.
As of version 5.3a of the COMSOL® software, the Nonlinear Structural Materials Module includes two of the most common material models for SMAs: Lagoudas and Souza-Auricchio. Using these material models in your simulation, you are able to define the austenite and martensite properties as well as the phase transformation properties of an SMA. You are also able to easily account for heat transfer in an SMA with a built-in coupling between the Heat Transfer in Solids and Solid Mechanics interfaces.
The Uniaxial Loading of a Shape Memory Alloy tutorial demonstrates using an SMA material model in the COMSOL Multiphysics® software.
In the tutorial model, a nitinol cylinder is subject to axial tension and three separate studies are performed:
- Parametric sweep, showing the pseudoelasticity effect at different fixed temperatures
- Prescribed displacement sweep, showing that the pseudoelasticity effect is a partially unloading and partially loading loop
- Shape memory effect, shown after increasing the temperature
The model indicates that there is a temperature-dependent stress limit for the SMA. When the axial tension reaches the stress limit, the material transforms from the austenite to martensite structure; i.e., a “forward” transformation (deformation) occurs.
Stress and strain of the SMA at different temperatures.
During the unloading of the axial stress, the reverse transformation occurs. This “backward” transformation occurs at a lower stress level than the stress limit for the forward transformation and shows the material returning to its original shape.
The stress and strain curves, which illustrate the shape memory effect in the alloy.
Next Steps
Learn about the specialized features and functionality for mechanical analyses in the Structural Mechanics Module, an add-on to COMSOL Multiphysics, by clicking the button below.
Note: The Lagoudas and Souza-Auricchio material models for SMA also require the Nonlinear Structural Materials Module, an add-on to the Structural Mechanics Module.
References
- G.B. Kauffman and I. Mayo, “Chemistry and History: The Story of Nitinol: The Serendipitous Discovery of the Memory Metal and Its Applications,” Chem. Educator, 2(2), 1997.
- J.M. Jani et al., “A review of shape memory alloy research, applications and opportunities,” Materials and Design, 56, 2014.
Slinky is a registered trademark of POOF-SLINKY, LLC.
Comments (0)