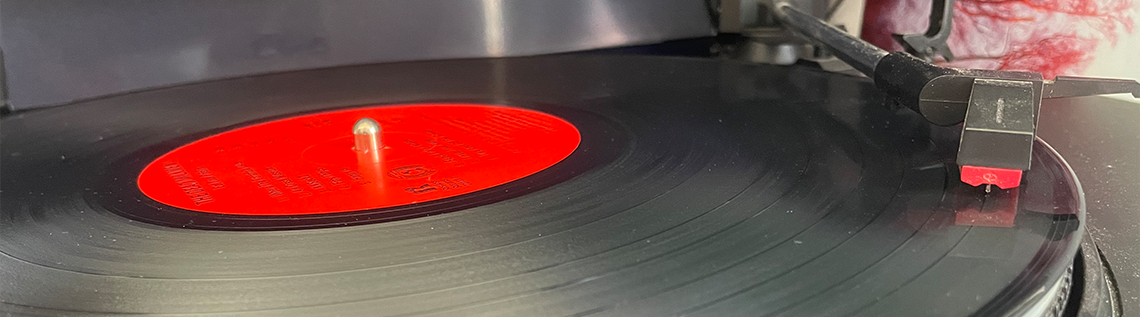
In the early 2000s, vinyl records were collecting dust — both in our attics and our collective consciousness. But then something curious happened. In 2008, music stores around the world started celebrating “Record Store Day”. Fast-forward to 2020, when vinyl record sales reached a record high, surpassing CD sales for the first time since 1986. As it turns out, vinyl records have a history and scientific background that is as fascinating as their nostalgia-driven resurgence in popularity.
The History of Vinyl Records
Cylinder Phonographs
In 1877, Thomas Edison was working on two of his most notable inventions, the telephone and telegraph. In the process, he invented the phonograph as a way to play back recorded sounds. In a June 1878 issue of North American Review, Edison wrote that he envisioned the “reproduction of music” as a future use of the device, as well as dictation, education, and telling time (like a verbal clock).
Thomas Edison and an early iteration of the phonograph. Image by Levin C. Handy — Library of Congress. Image in the public domain via Wikimedia Commons.
The Volta Laboratory, run by Alexander Graham Bell, made improvements to Edison’s designs during the 1880s, calling the enhanced device the gramophone. Instead of reading the sound from a wax cylinder like the phonograph, the gramophone operated via a hand-crank mechanism that turned a hard rubber disc on a flat plate. In 1887, German-American inventor Emile Berliner developed lateral-cut flat discs to be played on the gramophone, similar in use and appearance to the vinyl records we know today.
Emile Berliner with an early gramophone and lateral-cut flat disc record. Image in the public domain via Wikimedia Commons.
By 1892, phonographs and gramophones were being marketed to the public, with the former positioned as “entertainment offerings on brown wax“. However, the early wax cylinders used in phonographs could only store a two-minute recording of sound, and were costly and inefficient to produce.
In 1901, duplicate wax cylinders started to be mass produced. They were made from molds rather than individually engraved by a stylus, and used a harder type of wax. These cylinders were sometimes called “gold-molded” cylinders, because the gold electrodes used in the production process would give off a golden vapor. With this new process, 120–150 cylinders could be made at once.
78s
The flat disc records popularized by Berliner play at a speed of about 78 revolutions per minute (rpm), which is why they are called “78s” by most collectors. Improving on the quality of wax cylinders, these discs could store 3–5 minutes of sound per side. They were made from a shellac resin that feels a bit heavier and more brittle than modern vinyl records.
During World War II, shellac was hard to come by, so some 78s started to be pressed using vinyl materials instead.
“Modern” Vinyl
By 1930, the company RCA Victor launched the first commercially available vinyl long-playing record. Instead of 78 rpm, the playback speed for this modern record was 33⅓ rpm, and the record itself was 12 inches in diameter. This meant that the records could play a longer duration of sound. A rival company, Columbia, followed suit in 1948, releasing the 12-inch “long play” 33⅓ rpm microgroove record. RCA responded with a smaller record, at 7 inches, that plays a single song on each side at 45 rpm, called the “extended play”.
Today, recording artists still denote their releases as long plays and extended plays (LPs and EPs) — whether or not the music is available in a physical format!
By the 1970s, the introduction of compact cassette tapes (the only portable way to listen to music at the time) and eight-track tape cartridges caused vinyl to take a back seat. The introduction of CDs, digital downloads, and streaming services continued this trend.
Back in the Spotlight: A Vinyl Resurgence
Since the advent of Record Store Day in 2008, there has been a rising affinity for vinyl records over other mediums. Vinyl sales have steadily climbed, with a 46% growth in sales just from 2019 to 2020! This surge in demand has led to serious bottlenecks at record pressing plants around the world — some have up to 8 months of waiting time to get orders pressed and shipped!
Now that we’ve gone over the history of vinyl records and their boomeranging popularity, let’s take a look at how they play music, how they’re made in the first place, and the science behind the materials involved…
How Records Play Music
The way vinyl records are able to play sound through a record player is an interesting process. Vinyl records (also called lacquer discs) are pressed with grooved indentations (which may be where the expression “groovy!” comes from). These grooves act as a “fingerprint” for the sound waves from the original artist recording.
To play a record, you place it on a record player, which has a rotating base and a long, thin tonearm. The tonearm has a cartridge at the end, with a stylus made from either diamond or sapphire. As the record player spins, the stylus vibrates in the record’s grooves.
The cartridge at the end of the tonearm contains a piezoelectric crystal. When the stylus is vibrating in the grooves, it generates an electric signal through the cartridge. This signal is then fed out to the record player’s amplifier.
As the record plays, the stylus moves from the outer edge of the record to the center, typically at a speed of 33⅓ rpm, which gives 20–30 minutes of sound on each side. (Many recording artists put a lot of thought and effort into sequencing their albums so that the song at the end of Side A is more upbeat and dynamic, making you want to turn the record over and keep listening.)
A vinyl record on a record player, with the tonearm, cartridge, and stylus shown in the top right corner.
Audiophiles often harp on the fact that vinyl provides a much better listening experience than CDs or streaming services. Why is that? The difference may come down to analog versus digital recording. Vinyl is analog, meaning the grooves of a record are a physical representation of the actual recording. The other modern formats are digital, which means the recorded music is transformed into a set of discrete numbers. Perhaps this is why the sound of vinyl is often described as “warmer” or “more real” than digital playback — although this is often fuel for debate.
How Vinyl Records Are Made
The production process for vinyl records is time consuming, expensive, and starts way before the manufacturing room floor. First, the recorded music must be optimized for conversion into vinyl through a process called mastering. This is when specially trained sound engineers ensure that the levels, limiting, equalizing, and sequencing of the tracks are of optimal quality.
Next, a technique called lathe cutting is used to imprint the mastered files to a lacquer plate. A diamond stylus carves the grooves of the record directly into a master disc made of copper.
A technique called electroplating follows: The lacquered master disc is sprayed with a silver solution in order to fortify it against the pressures of mass replication, then placed in a nickel bath to create a “stamper” that has raised grooves to create the grooved indentations in the vinyl copies. Often, multiple master discs and stampers are made, especially when the plant needs to fulfill larger (>10,000) orders. Each stamper usually lasts for about 1500–2000 records before it wears down and can no longer be used.
After electroplating, the stampers are taken to a hydraulic press. A preheated blend of polyvinyl chloride (PVC) pellets are formed into solid pucks called “biscuits”, which are then heated to 148°C (300°F) and compressed inside the hydraulic press with more than 2000 psi for about 8 seconds each. The stamper acts like a waffle iron, pressing grooved patterns into the biscuits while flattening them.
A hydraulic press at a record pressing plant, manufacturing copies of the album As I Am by Alicia Keys. Image by David McClister — Own work. In the public domain via Wikimedia Commons.
The newly pressed records are cooled for another 8 seconds each in a water bath, and then they are trimmed and rounded into their final shape. The records also go through a final curing process, which is important to avoid warping later on.
Record plants generally create test presses before producing an entire batch of records. This way, record labels and independent artists alike can perform their own quality assurance before hundreds or thousands of faulty records are made.
Fun Fact: Why Black?
Records can be pressed in a seemingly endless variety of colors and patterns, making for rare editions — a collector’s dream.
White, dark purple, and sienna/umber variants of vinyl records from my personal collection.
However, vinyl records are most commonly pressed in black PVC, and the reason why could be explained by electrostatics, according to Furnace Record Pressing.
As it turns out, PVC is a natural insulator that builds up a static charge over time, and this charge can attract dust. Dust is a vinyl record’s worst enemy: It can accumulate in the grooves and wear down a record player’s stylus. Carbon black is added to the PVC blend to increase the overall conductivity of the material, which means less accumulation of static, and dust, on the record over time.
From personal experience, it also seems easier to spot a layer of dust on a black record, so you know to wipe it down before tossing it on!
Materials Science of Vinyl Records
The main ingredient in a vinyl record is not rhythm, melody, or soul — it’s polyvinyl chloride, a polymer made up of chlorine and ethylene. Ethylene is made by processing raw, hydrocarbon-based materials like petroleum, coal, and natural gas, while chlorine is manufactured by electrolysis of salt water in membrane cell electrolyzers. These two materials are combined to form ethylene dichloride, which is then transformed into a vinyl chloride monomer, or VCM.
Pure polyvinyl chloride in powder form. Image by LHcheM — Own work. Licensed under CC BY-SA 3.0, via Wikimedia Commons.
The final polymerization process involves converting the VCM into the actual vinyl polymer, PVC. Then, chemical modifiers are added into the mixture in order to achieve specific qualities in the finished product.
Molecular structure of the polymerization process for polyvinyl chloride. Image by Jü — Own work. Image in the public domain via Wikimedia Commons.
One aspect of PVC that makes it a great material for vinyl records is the fact that it is 10–20% crystalline. This means it is just strong enough to support the hollowing out of the record’s grooves during production, and that it can handle the applied pressure of the turntable’s stylus.
Additives
Although PVC makes up about 96% of a vinyl record, there are additional ingredients added to the mixture that are used to impart certain important properties. For example, stabilizers make up about 1.5% of a vinyl record’s materials. They make the resin mixture more robust. During pressing, stabilizers are used to neutralize the hydrogen chloride gas that is generated from the high temperatures of the hydraulic press’s steam.
Plasticizers make up less than 1% of the mixture. They improve a record’s flexibility and make it easier to match the grooves in the master disc during the manufacturing process. Also making up less than 1% are lubricants, which improve the flow of resin during pressing and also reduce friction on the record’s surface during operation.
Lastly, about 0.5% of the makeup is carbon black, which we’ve already mentioned reduces static buildup and also makes it easier to see scratches on the record’s surface. Sometimes, colorants and recycled vinyl from other records are added into the the carbon black mixture.
Looking Toward the Future of Vinyl Records
The music industry can be particularly unpredictable. Who would have guessed that a way to play music invented more than a hundred years ago would be booming in popularity today?
In terms of science, engineers are looking into ways to improve record players, record pressing technology, and the materials used to make records — all in a newfound attempt to make the process more environmentally friendly.
I can’t wait to see what is next for the world of vinyl music as we flip from Side A to Side B, and then back again!
Further Reading
- Read more about materials science applications:
- See other examples of how music and science come together:
Editor’s note: An earlier version of this blog post incorrectly stated that Columbia released the microgroove record in 1939. It has since been updated to reflect the accurate year in which this record was released, 1948.
Comments (2)
implant media
January 11, 2022Hi. This is a nice blog written about history of vinyl records
Implant media provides best quality custom vinyl records in Australia. Get Cd, Dvd, Blu-ray Duplication & Replication services, Promotional Usbs, custom Vinyl record Pressing, Business card printing throughout Australia
https://www.implant.com.au/services/vinyl-record-pressing/
Donn Rutkoff
December 16, 2023The CBS guy who headed up the creation of The 33 rpm vinyl Peter Goldmark wrote autobiography Maverick Inventor. From Austrian Jewish music family. He also involved in creati TV, color TV, video recording, cassettes.