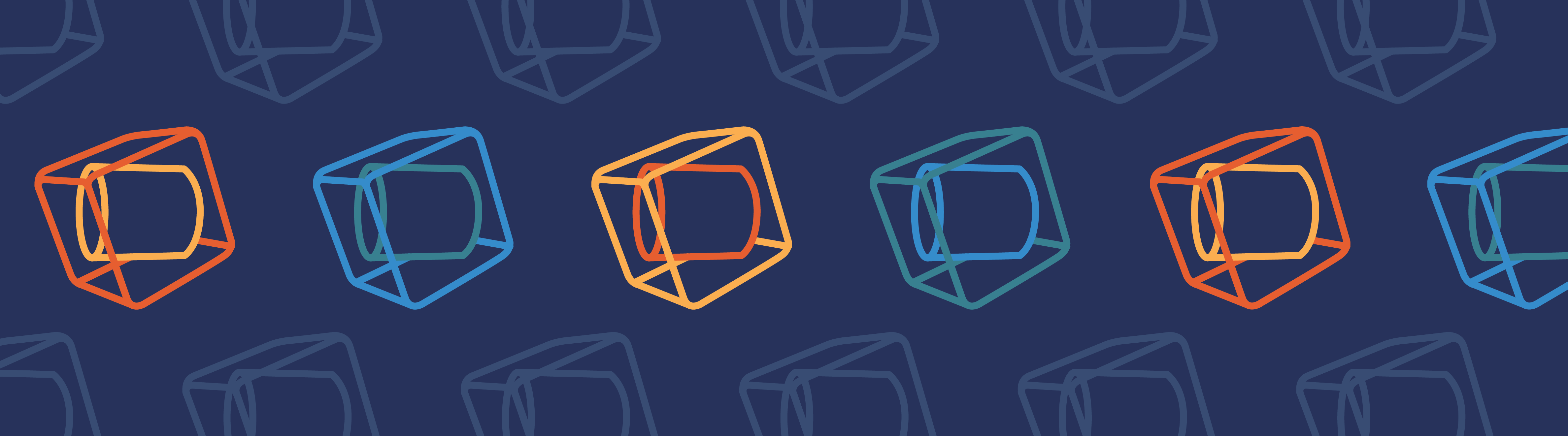
A while back, I blogged about a new feature made available in COMSOL Multiphysics 4.3b, the ability to create 2D models from the cross sections of 3D geometries. We are so excited for this new feature that we decided to make a video showing you how easy it is to use.
Taking Advantage of the Cross Section Feature
There are two main reasons for creating 2D models (if you think of a third, feel free to add it in comments section!). For symmetric and axisymmetric 3D models, the same geometry can be created in 2D, with a far quicker solution, as evidenced in the previous blog post. However, more often than not, geometries (and the real-world problem they represent) are not so simple. While you can’t always use this feature to replace the 3D model, you can use it to complement your model. That’s exactly what we aim to show in the video. The shell-and-tube heat exchanger model we use here is a complicated one; it combines CFD with heat transfer. Creating a cross section of the geometry to add a 2D model, we can disregard the heat transfer and air aspects of the model and focus solely on the flow characteristics of the water within the tubes. Solving the 2D model, we can view the velocity profile as well as the pressure in the tubes, and compare it to the 3D model’s results. The beauty of this feature is the ability to create your 2D model in the same file as your 3D model, for convenience and efficiency. Study the 2D results to adjust physics couplings, parameter ranges, small geometric features, mesh and solver settings, and apply them directly to the 3D model.
How to Create 2D Models from 3D Geometries
The video below shows you the process for using the cross section feature, and we encourage you to follow along by downloading the shell-and-tube heat exchanger model from our model gallery or from the model library (if you have the latest version of the software). You will need a COMSOL Access account to download the model — if you don’t have one, it’s just a simple form to fill out.
Video Transcription
COMSOL Multiphysics contains a feature to create 2D models from the cross sections of 3D geometries. There are two ways to take advantage of this feature: by creating 2D models from symmetric or axisymmetric 3D models for quicker solutions. Or by assisting in large, complicated 3D models, to investigate modeling strategies or examine parts of the model without having to solve in 3D.
This video will demonstrate the latter, by taking a heat exchanger model, examining the tube flow properties in a 2D cross section, and comparing it to the 3D model it belongs to.
I have opened up an example of a heat exchanger model from the model library to demonstrate this new feature. Here we have a 3D model of a shell and tube heat exchanger cut in half.
First, we need to do specify the cross-section that will be our work plane. We want it in the x-z plane, at 0.025 meters from the origin along the y-axis.
Now we want to model the flow characteristics on this work plane and so can select the fluid flow to be single phase, and described by the k-epsilon model. Select stationary for the study type, and deselect non-isothermal flow from this study, as we are initially only looking at the flow profile.
With our second model specified, we can add the cross-section from the 3D model to be the model geometry. The work plane created earlier is automatically selected, where there is a dropdown menu in case there had been multiple work planes created. Click build all to create the 2D model with the physics already specified.
Open the material browser, and in the built in materials node, add water to our model.
In the turbulent flow node, clear the selection box, and add only domain 1, which is the collection of tubes in the heat exchanger. Then add an inlet on the left most boundary, and enter the parameter u_water for the velocity, previously defined in a parameter list.
Finally add an outlet to the right most boundary, which specifies the pressure field to be relative to this point.
Right click the study two node to compute the model. COMSOL generates 3 default plots. We will investigate the velocity plot, and compare it to its 3D counterpart.
The total simulation time for this study is 5 minutes and 40 seconds, as opposed to a much longer time for the 3D model.
To compare the results from our 2D model with the 3D model, we can create a cross section of the solution from the 3D model, that only shows the velocity profile in the tubes. We use the same settings for modifying the slice plot as we did for the original workplane. And as you can see, the results show the same type of profile and are in the same scale. To show this more, you can plot the 3D model in a new window and view the results side-by-side.
You can investigate the results and parameters of the 2D model, such as physics couplings, parameter ranges, small geometric features, mesh settings, and solver settings, that you could then apply to the 3D model for a faster, more accurate solution.
For more information, visit our website.
Comments (8)
Shadi Hamdan
June 11, 2013How long it takes for the simulation in the 3D case? I ran this model in a laptop with 8GB memory but it always return an error of low memory! and stop the similation.
any comments please?
Andrew Griesmer
June 11, 2013 COMSOL EmployeeThe model has 1 million DOF, and with 16 GB’s RAM, the 3D model takes 2 hours to solve. With a user-defined mesh, it is possible to get a decent solution (but less accurate) with 200k DOF, and it takes only 10 minutes on the same machine. Try making the mesh courser to solve the model on an 8 GB machine.
Sri Puranam
August 5, 2013Is there a method for copying the 3-D mesh onto the 2-D model? I would like to use the flow solution from the 3-D model as an input for the 2-D model – can I do this?
Andrew Griesmer
August 7, 2013 COMSOL EmployeeYou can use the General Extrusion model coupling operator to map a solution from a slice of a 3D simulation and use it in a 2D model. You can also do the reverse, and project 2D results onto the 3D space.
Safiya Al Turabi
August 18, 2013What about the non-isothermal heat exchange problem in 2D?
Is there a tutorial or a video about the whole non-isothermal problem?
I would like to understand how to implement it in 2D.
Andrew Griesmer
August 21, 2013 COMSOL EmployeeOur model gallery contains a tutorial for a non-isothermal heat exchange problem in 2D and can be found here: http://www.comsol.com/model/turbulent-flow-through-a-shell-and-tube-heat-exchanger-1879
This is not the same model but I hope it helps!
Johnson Singh
November 19, 2014When comsol performs the study for 2D component case, does it process with respect to the meshing parameters defined in the 3D case or with respect to the meshing that appears in the 2D component case? I mean can the meshing define in the 2D component case alter/improve the overall result?
Regards,
Johnson
Andrew Griesmer
November 19, 2014 COMSOL EmployeeHi Johnson, the 2D and the 3D models are independent, no information is
passed between them. The meshing defined in the 2D case cannot improve
the overall result in the 3D model.