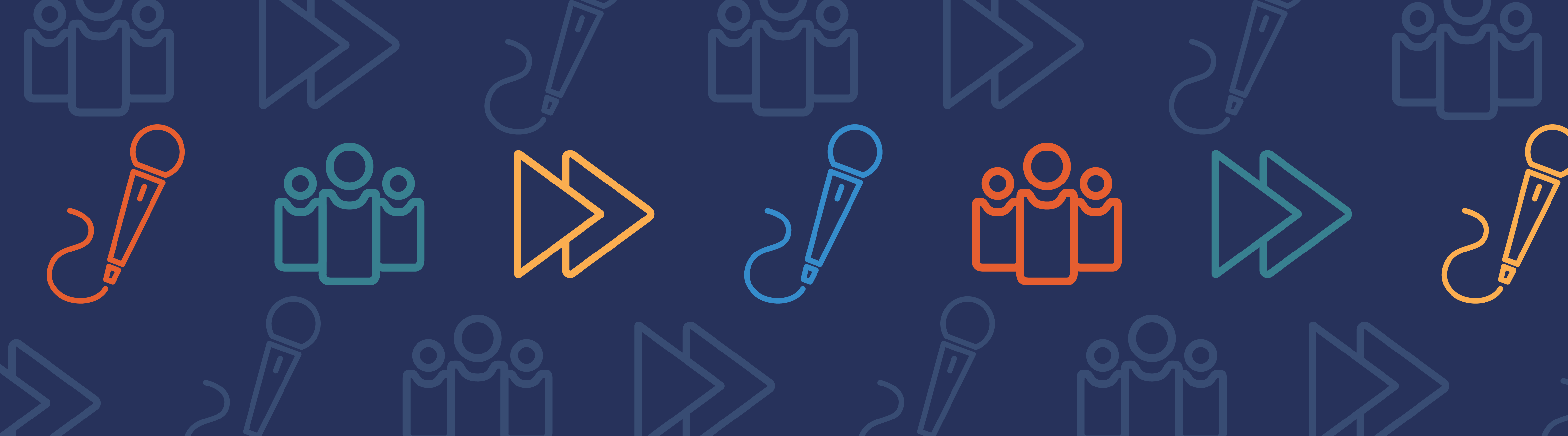
It’s no news that accurate mechanical analysis is key to avoiding product failure and manufacturing issues. What may be new is how you do it. Simulation software offers a modern approach to analyzing mechanical component and system designs. Watch this video to learn how COMSOL Multiphysics enables you to speed up time-to-market and optimize product designs.
Video on Modeling Mechanical Applications
We recently published a new resource for all of you mechanical engineering folks who are looking to learn more about accelerating time-to-market and improving designs with simulations. The showcase is called “Analyzing Mechanical Systems and Designs” and contains videos, models, case studies, and more on the subject.
I would like to share one of the videos from that resource with you here. Below the video, you will find the accompanying transcription, in case you would prefer to read instead of watch it.
Mechanical Analysis: The Modern Start of the Product Life Cycle
Video Transcription
The more precise and explicit your simulations of mechanical parts and assemblies are, the less chance for product failure and delayed manufacturing runs.
And for accurate and real-world simulations, this means considering all of the different physical phenomena that affect your mechanical system and its components. As computational resources become cheaper and increase in ability, simulation is becoming a standard feature in the engineer’s workflow.
Backed by robust and accurate meshing and solving algorithms, we at COMSOL have built a suite of modules for structural analyses, including linear elastic and multibody dynamic analyses of parts and assemblies, as well as nonlinear material modeling capabilities. These include elastoplastic, viscoplastic, creep, and hyperelastic material models, as well as ones for geomechanical applications. These can be combined with modules for other mechanical applications, like heat transfer, to simulate thermal stress and deformation; acoustics, to simulate acoustic wave propagation in solids and fluids; and fatigue analysis for repeated loads in the low-cycle and high-cycle regimes.
The modeling of structural stress fields and strains are influenced by: physical constraints, loads and forces, joints and contact between objects, and material properties.
Maintaining a consistent modeling process with geometry synchronization, import or creation, adding and modifying material properties, defining physics and boundary conditions, meshing the geometry, running the analysis, and postprocessing your results, we seek to find the perfect symbiosis between functionality and ease-of-use.
“COMSOL fits perfectly into your engineers’ workflow. They will bring in a design through an import of CAD or ECAD, they’ll do analysis and then postprocess that, and then be able to optimize the design based on that analysis.”
COMSOL Multiphysics is compatible with major CAD packages, offering full associativity between CAD modeling and multiphysics simulation, promoting collaboration between individuals.
Yet, the real strength of the software is the inclusion of multiphysics applications that are prepackaged for you within COMSOL Multiphysics, such as piezoelectric and acoustic structure interactions, electromechanical couplings, fluid-structure interactions, and thermal and electric contact. Often, a multiphysics model is the only credible simulation for your real-world mechanical application.
Scroll down to learn more.
Access the “Analyzing Mechanical Systems and Designs” Resource
The above video is just one piece of content available to you in the “Analyzing Mechanical Systems and Designs” resource. Also showcased are user stories, models, animations, and video tutorials.
You can learn more about modeling the following applications:
- Structural analysis
- Nonlinear materials
- Thermal stresses and deformation
- Acoustics
- Multibody dynamics
- Fatigue
- CAD integration and optimization
Explore how your company can leverage COMSOL Multiphysics software to analyze mechanical systems and designs:
Comments (0)