Chemical Reactions and Soot Build-Up in a Diesel Filter
Application ID: 1394
In this tutorial, a filter system for a diesel engine is modeled, including a soot layer development and oxidization. The build-up of the layer is held in check by both catalytic and non-catalytic reactions, where carbon is oxidized to carbon monoxide and carbon dioxide, which in turn passes through the membrane.
A filter system's efficiency and durability is closely related to the manner in which it removes soot deposits from the porous filter walls. One approach involves introducing cerium additives to the fuel. Cerium oxide species are subsequently present in the soot layer, acting as a catalyst in carbon-oxidation reactions. Under these conditions, it is possible to remove carbon deposits in the filter without increasing the exhaust temperature. Five reactions and their accompanying kinetics are included in the mass balances.
Two strategies are used to investigate this system. First, an ideal model of the system using the Reaction Engineering interface is utilized. This includes modeling of an ideal tubular (plug flow) isothermal reactor with the reaction kinetics only accounted for. The second strategy uses a space-dependent (2D) approach using four physics interfaces in the Chemical Reaction Engineering Module:
- Free and Porous Media Flow (fluid flow)
- Transport of Diluted Species (material balance)
- Heat transfer in Fluids (energy balance)
In this part the position of the top boundary, as a result of the soot build-up, is also explicitly solved for using a Moving Mesh feature.
Results for the first strategy show that the catalytic reactions dominate the oxidation of carbon, which decreases with increasing temperature. Further, results from the 2D model show that although the oxidation of carbon is an exothermic reaction, the catalytic steps are endothermic. Additionally, the carbon oxidation is not sufficient to keep the soot layer from growing.
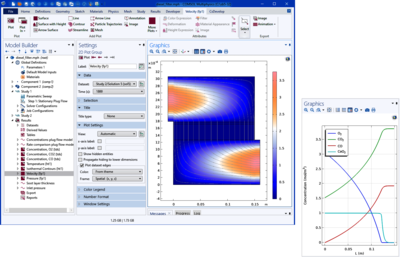
This model example illustrates applications of this type that would nominally be built using the following products:
however, additional products may be required to completely define and model it. Furthermore, this example may also be defined and modeled using components from the following product combinations:
The combination of COMSOL® products required to model your application depends on several factors and may include boundary conditions, material properties, physics interfaces, and part libraries. Particular functionality may be common to several products. To determine the right combination of products for your modeling needs, review the Specification Chart and make use of a free evaluation license. The COMSOL Sales and Support teams are available for answering any questions you may have regarding this.