Acoustic Upside-Down Levitator with a Solid Sample
Introduction: Acoustic levitators are used to levitate small samples (ca. 0.01 - 6 mm) at a stable position in a gas or liquid environment. Acoustic levitators were first developed und used for experiments in space (1970s, by NASA / ESA), the application later became terrestrial (1990s). Meanwhile acoustic levitators are widespread.
I present a practical model, to show basic properties and interactions and some additional phenomena und aspects in a stepwise approach to the realistic world of acoustic levitators.
In this levitator model the millimetre-sized spherical sample is located (in air environment) below the piezoelectric transducer (mechanical coupled resonator), which radiates the inaudible sound of 22 kHz downwards against the reflector. The transducer is based on a sophisticated 20 kHz model, designed by E.-G. Lierke. I used that version in 1991 at the Battelle Institute (Frankfurt/Main, Germany).
How COMSOL Multiphysics® simulation software was used:
In the 1st development step of the FEM model, only the transducer was set up and the Structural Mechanics Module was used for a static study. In this ´transducer assembling step´, the piezo rings of the transducer are axially preloaded by the central clamping screw (Bolt Pre-Tension). With open piezo electrodes, the resulting piezo voltage indicates the mechanical preload in practice.
In the 2nd development step, an Eigenfrequency study inspects the undamped, axial natural oscillation of the prestressed piezoelectric transducer. By adjusting the transducer geometry, the resonance frequency was tuned to 22 kHz and the velocity node placed into the level of the fixing flange. This Eigenfrequency study also helps, to exclude undesired tilt and pendulum oscillations of the transducer.
A frequency domain study (Harmonic Perturbation) vibrates the prestressed piezoelectric transducer to harmonic oscillations (with use of the AC/DC Module). The frequency scan over the resonance range also shows the internal mechanical (Rayleigh) damping in the transducer material in the shape of the amplitude resonance curve (with reasonable damping values taken from e.g. annealed high-grade titanium alloy).
The Acoustics Module was used, to calculate the Acoustic-Solid Interaction (Frequency Domain) between transducer, acoustic levitation field, reflector and solid sample. With Pressure Acoustics (acpr) the levitation forces were deduced from the acoustic radiation pressure on the sample surface.
Results: The current available model contributes to understand the reality of acoustic levitation and helps to improve acoustic levitators for future applications. The model enables the user to study basic properties, like - the frequency-dependent power transfer on the way from the piezo electrodes into the levitation sound field, - the mechanical stress and deformation of the ultrasonic transducer, - the values for transducer amplitude, sound pressure level and acoustic radiation forces to levitate lightweight up to heavy samples, and - the force progression in case of a sample position change.
Furthermore, the model shows some additional phenomena, such as the resonance shift of single-axis acoustic levitation due to the presence of a rigid spherical sample.
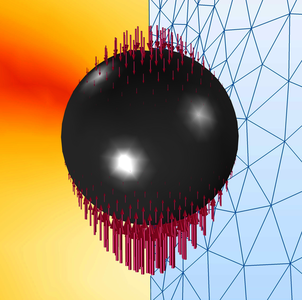
Download
- holitzner_presentation.pdf - 2.26MB
- holitzner_poster.pptx - 2.33MB
- holitzner_abstract.pdf - 0.04MB