Advanced FEM Simulation of Loudspeaker Performance: The Impact of Cone and Surround Materials
Finite Element Method (FEM) simulations are vital in the design of loudspeakers, providing an efficient alternative to traditional trial-and-error methods. This study aims to advance the understanding and optimization of loudspeaker design focusing particularly on the influence of various cone and surround materials. The objective is to understand how different materials impact the acoustic characteristics of loudspeakers and to offer insights for optimized design strategies.
The study began with an analysis of loudspeaker materials, involving both empirical measurements and COMSOL Multiphysics® simulations. Material samples were excited through physical measurements to determine their resonance frequencies. Following this, a model was built applying the COMSOL® Solid Mechanics interface to simulate these excitations, using an eigenfrequency study coupled with an optimization function to compute the Young’s modulus of the materials. The materials tested included various types of paper, fiberglass, paper with Kevlar and paper with mica for cones, as well as rubber, cloth, and foam for surrounds. This initial phase provided detailed insights into the mechanical properties of the materials, this is important for materials with natural variations in their mechanical behavior, and essential for accurate loudspeaker modeling.
Secondly, a comprehensive study was conducted on four loudspeakers, built using membranes selected from the materials study. The loudspeaker models utilized a hybrid approach integrating FEM with lumped parameter models. Various COMSOL® interfaces were employed: the Electrical Circuit interface for the lumped parameter modeling of the magnetic circuit and the Solid Mechanics interface for simulating the loudspeaker moving parts. The acoustic propagation was modeled using the Pressure Acoustics interface, including a Poroacoustic modeling of the loudspeaker spider, a Perfectly Matched Layer for the modeling of an infinite acoustic domain, and a Thermoviscous Boundary Layer Impedance modeling of the magnetic gap. The mechanical and acoustical domains were coupled using the Acoustic-Structure Boundary interface.
Empirical measurements of the loudspeakers were then conducted using different testing modules to determine small signal parameters, mechanical vibration visualization, and acoustic response measured in a semi-anechoic chamber. This data was used for a robust comparison of measurements and simulations. An in-depth look was made into mismatching behaviors at specific frequencies. This allowed to understand the source of the mismatch and its concern with the modeling of the materials, as well as how each model could be adapted to better match measurements.
The results found that with this method a significant matching of simulation with real life performance could be made. This gives insight on the method for modeling each material used. One significant finding was the frequency dependence on the Young’s modulus of a fiber glass cone. Insights like these allow for more accurate modeling of loudspeaker materials and lay a foundation for future exploration of novel materials with enhanced acoustic properties and mechanical durability, guiding the development of more reliable and high-performance loudspeakers.
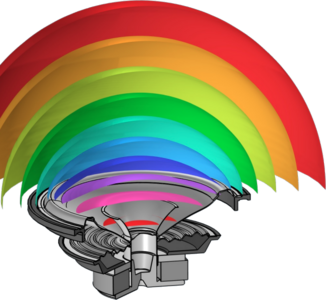
Download
- replogle_9711_poster-1.pdf - 2.04MB
- 1_adriane_replogle.pdf - 2.99MB