Design and Analysis of Fluid Structure Interaction for Elbow Shaped Micro Piping System
Fluid and structure Interaction analysis can be applied to versatile fields of engineering applications, helps in understanding the affects of one material on other, thereby reducing the effect of physical parameters like nonlinear response, vibration in flow channel etc. Rapid development of technology led to the application of this Fluid-Structure Interaction (FSI) in Microfluidics based devices that were widely used in Bio medical, Printing Technology and Aerospace etc. The combination of fluid flow analysis with change in solid mechanics for an elbow shaped micro pipe line system having obstacle in its flow channel is shown in Figure 1. This model can be applied for Industrial/ Medical research applications for designing micro pipes, micro structures for transport of drugs etc.
COMSOL Multiphysics® software helps in designing using free hand and interfacing the various physical parameters with the base model. Geometry deformation takes places due to the effect of obstacle placed in flow channel. This deformation can be understood from the Von Mises Stress plot with respect to velocity magnitude. Fluid flowing with greater inlet mean velocity will cause an impact on the obstacle that was placed in the channel there by displacing its original position, which can be analyzed by the maximum/ minimum mesh displacement. Flow and stress interaction plays an important role in this model which can be analyzed using COMSOL Multiphysics®.
Results: Using COMSOL Multiphysics® software, two kinds of studies has been explored i.e., study 1 is time dependent, based on the fluid flow and its corresponding stress on the structure. Whereas study two gives the deformation results after interaction with the structure and the pressure distribution in the flow channel. In this MEMS based Elbow shaped micro piping system was designed with two different models. Model one was analyzed using one obstacle, whereas model two results for two obstacles in the flow channel. Mesh velocity and mesh displacement in X direction with respect to inlet mean velocity for single obstacle placed in micro channel were shown in figure 3. Flow vortices where introduced after the first obstacle, when two obstacles were placed in a single flow channel, which results in greater mesh displacement when compared to its counterpart that is shown in Figure 4.
Simulation for designed MEMS model is done by changing the number of obstacles in the flow channel and by varying the inlet mean velocities. Obstacle shapes can also be changed from rectangular which is used in base model to circular, elliptical etc and the flow channel can be positioned in inclined way so that the effect of flow in vertical direction is analyzed. Obstacle is placed in different positions i.e. at the input side, middle of channel and at the output of pipe along with the junction points that helps in better understanding the micro structure interaction with fluid flow. This technique can be used in bio-medical applications for the analysis of blood vessel and its interactions with the flowing blood.
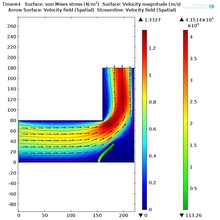
Download
- rajesh_presentation.pdf - 1.58MB
- rajesh_poster.pdf - 0.53MB
- rajesh_abstract.pdf - 0.42MB