Modeling defect detection in deep-seated tendons of prestressed concrete using magnetic flux leakage
The integrity and safety of reinforced concrete structures are of paramount importance in civil engineering. Detection of flaws in prestressed tendons, especially those buried at critical depths greater than 20 cm, presents a significant challenge. Magnetic flux leakage (MFL) is a non-destructive testing method widely used for detecting near-surface defects in ferromagnetic materials. This study employs COMSOL Multiphysics to simulate and optimize MFL flaw detection for tendons embedded in concrete at more substantial depths, incorporating ferromagnetic hysteresis effects to enhance the accuracy and reliability of detection. The primary objective of this study is to determine the optimal experimental setup for detecting steel tendons in concrete using MFL at depths exceeding 20 cm. Key goals include: 1. Incorporating ferromagnetic hysteresis to accurately reflect the magnetic properties of the tendon. 2. Evaluating different sensor configurations and magnetizing coil arrangements to optimize practicality, detection sensitivity and resolution. The simulation was conducted using COMSOL Multiphysics, leveraging its Electromagnetics Module to model the MFL detection system, comprised of a u-shaped DC electromagnet and a Hall effect sensor. The study began with the creation of a 2D model of a concrete block containing a tendon at a depth of 20 cm and beyond. The tendon was modeled as a ferromagnetic material with specified hysteresis properties to mimic real-world conditions. 1. Magnetic Modeling • The magnetic properties of the tendon, including coercivity and remanence, were incorporated using the Jiles-Atherton model to simulate ferromagnetic hysteresis. This approach allowed for accurate representation of the magnetic behavior of the tendon under varying magnetizing fields. 2. Sensor and Coil Configuration • Various configurations of magnetizing coils and MFL sensors were tested to determine the setup that offers the maximum flux leakage signal. Parameters such as coil size, number of turns, current amplitude, and sensor placement were systematically varied and analyzed. 3. Study Type • The simulations were performed in the static time domain to simplify the computational complexity and focus on steady-state magnetic flux distributions. This approach enabled detailed examination of the magnetic flux leakage patterns and their correlation with the position and orientation of the tendon. 4. Signal Processing • The simulated MFL signals were processed to extract key features indicative of the tendon's presence and condition. Signal enhancement techniques, such as filtering and Fourier transform, were applied to improve the detection accuracy. The inclusion of ferromagnetic hysteresis significantly improved the realism of the simulation, capturing subtle variations in magnetic flux leakage that are critical for detecting defects in deeply submerged tendons. The findings show that accuracy is an important factor when modeling the ferromagnetic hysteresis in MFL simulations. A substantial improvement in flaw detection capability was reached by means of the simulation-based optimization of the setup, with MFL signal strengths above the threshold value required for detection at depths greater than 20 cm. These results provide valuable insights into the design of MFL detection systems for deep tendons, highlighting the critical factors that influence detection sensitivity and resolution.
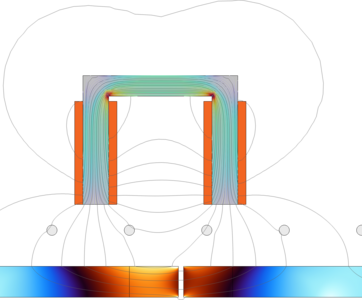