Modeling of Arc Welding Power Source
Introduction: The main objective of the present work consists in modeling an arc welding heat source to allow predict peak temperature and cooling rate at specific points. The filler metal was deposited on a plate of 32mm thick with no chamfer, in bead on plate configuration, using five different preheat temperatures: -30°C, 30°C, 100°C, 150°C and 200°C.
Use of COMSOL Multiphysics® software: COMSOL Multiphysics software was used for the implementation of the entire model. The geometry was built in SolidWorks® and exported to COMSOL Multiphysics. A table was built containing the welding parameters and constants needed to implement the model. The Goldak’s double ellipsoidal heat source model was implemented through the use of two functions to control the heat distribution and a time dependent variable to impart motion to the heat source. The Heat Transfer Module was used for the Heat Transfer in Solids physics interface and the time dependent study option.
Results: As results, the peak temperatures and the cooling rate at points of interest were obtained. The comparative graphics of the numerical weld thermal cycle and the experimental weld thermal cycle can be seen in the Figure 1. It is also possible to understand how the temperature distribution throughout the body occurs, Figure 2 and Figure 3. The numerical results show good agreement with experiments.
Conclusions: Through this study, it is possible to determine the feasibility of using the software for pre-determining the peak temperature and the cooling rate due to electric arc welding. These data are useful to estimate the best welding parameters. Moreover, it is possible to have some idea of the mechanical properties and final microstructure in the evaluated region.
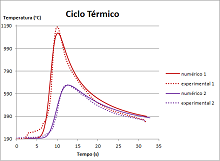
Download
- Tschoepke_presentation.pdf - 0.89MB
- Tschoepke_abstract.pdf - 0.18MB