Numerical Simulation of Pool Film Boiling Heat Transfer during Quenching of Heated Cylindrical Rods
This research studies possible ways to mitigate failure of a nuclear reactor, in which the coolant supply to the nuclear core has been compromised, known as Loss of Coolant Accident (LOCA). One possible way to decrease the severity of the incident is to quickly quench the fuel rods in water. The heat transfer and hydrodynamic mechanisms involved in this quenching process are numerically simulated using COMSOL Multiphysics.
The thermo-fluid-dynamics of the quenching process involves a very complex phenomenon due to the cooling mechanism. When the heated surface is plunged in the pool, a water vapor film completely covers the hot rod where the liquid is not able to be in direct contact with the solid surface. This regime of heat transfer is known as film boiling. As the rod loses heat by evaporating water, eventually the liquid water comes into physical contact with the rod and the vapor film breaks at the tip. The quench front, that is, where the liquid is reestablishing contact with the rod, moves steadily upward leading to rapid bubble formation, called nucleate boiling. Finally, it makes way for natural convection to dominate the cooling process.
The focus of this research is to study the effects of material properties and liquid subcooling on the quenching process particularly regarding the vapor film morphology around the surface of the rod. The initial temperature of the rod is well above the minimum film boiling temperature (Tmin) to sustain a stable vapor film around the rod. As seen in Figure 1, the rod is vertically plunged into a quiescent pool of water that has various subcooling temperatures. At the given time, film boiling regime occurs where the vapor film (phase 1) completely surrounds the heated cylindrical rod.
Heat transfer in fluid and turbulent flow models are used to simulate the problem. The initial temperature of the rod is specified to be 550 degrees Celsius and the initial temperature of the water in the pool varies between 90 to 98 degrees Celsius. The simulated fuel rod has a diameter of 9.5 mm and a length of 25 cm. The pool diameter is 30 cm and its height is 50 cm. The vapor film thickness is expected to alter as the thermal properties of the rod surface and liquid subcooling change. Thus, the surface temperature and the surface heat flux will vary in the film boiling regime.
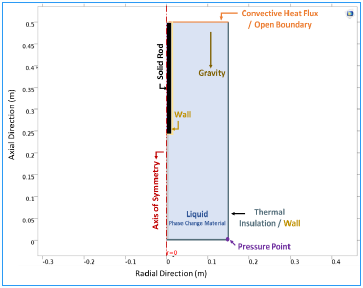
Download
- ebrahim_presentation.pdf - 1.57MB
- ebrahim_poster.pdf - 0.53MB
- ebrahim_paper.pdf - 0.71MB
- ebrahim_abstract.pdf - 0.05MB