Simulation of heating of a beam shaping spatial light modulator in Area Printing® metal 3D printing
A critical constraint in handling high power laser beams approaching 100kW of peak average power is thermal management due to laser absorption. Seurat Technologies uses a unique, optically addressed spatial light modulator (OASLM) with liquid crystals to dynamically shape laser beams for rapid, high resolution metal 3D printing in their Area Printing® technology[1]. COMSOL finite element analysis simulation software was used to derive the heating and temperature distribution within the OASLM liquid crystal layer that can impact key refractive properties, including the temperature dependent birefringence. The simulations were necessary to inform OASLM designs of the cooling scheme and configuration using liquid coolant flows in the turbulent regime, especially when temperature measurements are not readily accessible.
The laser induced heat generation and heat transfer problems were resolved with coupled radiative laser beam in absorbing media and non-isothermal turbulent coolant flow simulations. The simulations were also benchmarked experimentally using the optically measured first order transition expected from the liquid crystal for given flow and laser power conditions. The results enabled us to assess the suitability of the system OASLM cooling to ensure the required performance of the 3D laser Area Printing system, while validating the materials properties and source term measured independently and used as input to the model. The validated model will be used for reliable optimization of both material selection and thermal management in future higher power implementations of the laser metal 3D printers at Seurat.
[1]https://www.seurat.com/area-printing
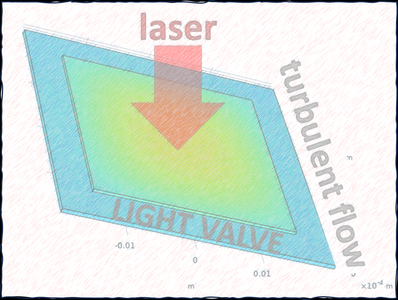