Simulation of Mass and Heat Transfer in Active Carbon CO2 Storage Tank During the Charging Process
In our dynamic energy landscape, it is increasingly important to utilize energy efficiently and minimize waste. To achieve this, advancing our research beyond traditional battery storage, which has numerous limitations, is crucial. One promising solution is compressed gas energy storage. While already used with air, this energy storage solution has energy density limitations. Energy storage by carbon dioxide (CO2) compression presents a better solution but requires storing CO2 after turbine discharge. Traditional liquefaction is energetically consuming, so alternative storage methods are needed. One of the methods involves adding adsorbents to a low-pressure CO2 storage tank to improve its storage capacity.
The present work aims to simulate the dynamic performance of a carbon dioxide (CO2) storage tank used for low-pressure gaseous CO2 storage in compressed CO2 energy storage (CCES) systems.
The effect of heat and mass transfer phenomena within a CO2 storage tank filled with activated carbon on the adsorption dynamics of the tank is modeled using COMSOL Multiphysics® software. The model is based on a set of partial differential equations (PDEs) governing the conservation of mass, momentum, and energy inside the tank. These PDEs are numerically solved using the finite element method. The research focuses on an axisymmetric model of a 5-gallon CO2 storage tank during the charging process at room temperature (298 K) and a charging pressure of 5 bars. The primary objective is to analyze the pressure and temperature changes and their distribution throughout the tank during this process. To achieve this, a realistic tank wall geometry is selected to account for conductive heat transfer between the tank wall and the environment, enabling a detailed analysis of temperature variations both axially and radially. The impact of the packed bed structure on storage capacity is explored, considering the interplay between adsorption and heat transfer. There are three porosities considered: particle, bed, and total porosities. Flow resistance is calculated using Darcy's law to determine the charging resistance. The Dubinin-Astakhov (DA) model, employed within the Chemical Reaction Engineering Module (CREM), describes the CO2 adsorption phenomena in activated carbons, facilitating the calculation of the storage process through mass and heat balances.
Regarding the simulation results, a rapid initial temperature increase, attributable to the exothermic nature of the adsorption process, is observed and followed by a gradual decline as the system approaches equilibrium. The pressure increment from 1 to 5 bars substantially influences the adsorption dynamics, with pressure changes having a more pronounced effect than temperature variations. Once the system stabilizes, a uniform temperature distribution is achieved throughout the tank.
In conclusion, this research employs finite element analysis to model the heat and mass transfer in CO2 storage tanks with activated carbon during the charging process. The insights gained are anticipated to enhance the design and operation of compressed CO2 energy storage systems, contributing to more efficient and sustainable energy storage solutions. The broader implications of this work include improved energy storage technologies, supporting efforts to reduce carbon emissions, and promoting renewable energy integration.
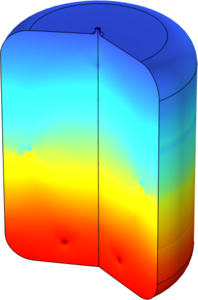