Temperature simulation of the Bridgman process as a basis for microstructure simulations
The Bridgman process is used in the production of single crystal superalloys for use in high temperature applications. The mechanical properties of these superalloys are strongly influenced by the microstructure that is formed during the solidification. The formation of the microstructure depends on the thermal conditions at the solidification front. It is mainly influenced by the thermal gradient and the cooling rate. Therefore, temperature simulations were carried out to determine these parameters as a function of casting conditions and component geometry.
The modelling setup for the temperature simulation in the COMSOL software is as follows. The calculation used the multiphysics of heat transport in solids and liquids, as well as the physics of non-isothermal flow to account for convection effects in the melt. In the Bridgman process, the component is cast in a ceramic mold which is heated in a furnace and drawn through a temperature baffle as it is shown in Figure 1. In the built model, this process is simulated by changing an external temperature field over time. The process takes place in a vacuum. Therefore, only radiation is considered for heat transfer on the sample surface.
As a result, the local temperature gradient and cooling rate, which determine the local solidification conditions, is determined. This is done for a variety of different casting conditions (sample withdrawal rates from the furnace), as shown in Figure 2, and for a variety of sample geometries (sample wall thicknesses), as shown in Figure 3. In addition, the formation of the isothermal liquidus temperature is studied in terms of its shape. This is necessary because a planar solidification front is required to grow a single crystal. For a variety of withdrawal rates and wall thicknesses, the solidification front curves at the edges as it is shown in Figure 4. This change from a planar solidification front increases the risk of nucleation of new grains, which should be kept small. In summary, this model can be used to determine both the thermal conditions for microstructure formation and the useful casting conditions to minimize the risk of nucleation.
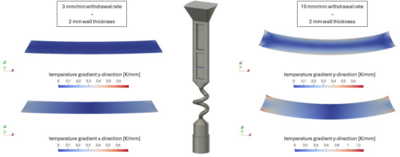
Download
- bohm_10691_poster.pdf - 2.01MB