Thermal Modeling for On-Interposer Thermoelectric Sensors
This paper summarizes the main features of the on-interposer micro-thermoelectric sensors (hereafter denoted by µTES) derived by means of simulations done with COMSOL Multiphysics® software. µTES are thermal sensors based on the Seebeck effect which converts thermal flow into electrical signal. They are constituted of several p-n junctions electrically connected in series and thermally in parallel. These sensors are developed in the framework of the European project STREAMS under Grant Agreement n° 688564 (www.project-streams.eu). They are used to detect hot points in microelectronic devices, and so manage the thermal flow in such environments. The geometrical design of these devices (area, junctions’ number, lines width and spacing, etc.) is critical to obtain the best performances, i.e. the highest sensitivity with the lowest response time. Two different thermoelectric (TE) materials have been tested: poly-SiGe and silicide-based Quantum Dots SuperLattices (QDSL). µTES are located near a Thermal Test Chip (TTC) used as a hot source. Specific architectures of the µTES environment have been studied to achieve the highest temperature difference and therefore the highest electrical supplying. Moreover, two kinds of simulations have been carried out to investigate the influence of the thermal input: by temperature or by thermal flow. The results of different simulations will be detailed and commented.
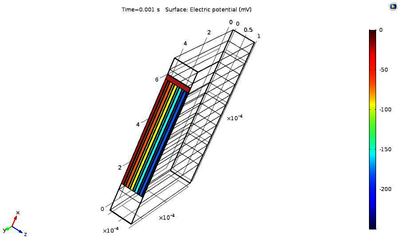
Download
- morel_presentation.pdf - 1.05MB
- morel_paper.pdf - 0.66MB
- morel_abstract.pdf - 0.06MB