Heat Pipe with Accurate Liquid and Gas Properties
Application ID: 90311
Heat pipes are designed to transfer heat efficiently through vaporization, mass transfer, and condensation of a working fluid. They are found in a wide variety of applications where thermal control is of importance, with cooling of electronics being a prominent example.
Inside a heat pipe, the temperature difference between the hot and cold sides together with the temperature dependence of the vapor pressure, induce a pressure difference across the vapor chamber. The pressure difference, in turn, drives the vapor from the hot to the cold side. The vaporization acts as a heat sink at the vapor–wick interface at the hot side, and conversely, the condensation as a heat source, at the cold side. This model demonstrates how the laminar flow in the vapor chamber of the heat pipe can be coupled to the liquid phase transport through the porous wick, and how thermodynamic properties of water can be obtained from the database in the Liquid & Gas Properties module. The importance of vapor transport is compared to the conductive heat transfer in the pipe wall. The former dominates the latter by several orders of magnitude.
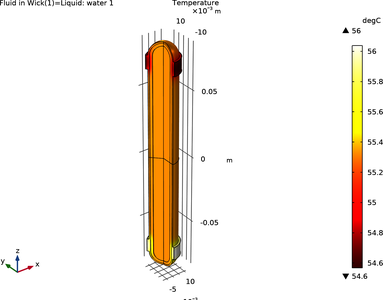
- heat_pipe.pdf - 0.94MB
- heat_pipe_parameters.txt - 0MB
- heat_pipe.mph - 34.8MB
- heat_pipe_parameters.txt - 0MB
- models.chem.heat_pipe.pdf - 0.82MB
- models.lgp.heat_pipe.pdf - 0.82MB
This model example illustrates applications of this type that would nominally be built using the following products:
however, additional products may be required to completely define and model it. Furthermore, this example may also be defined and modeled using components from the following product combinations:
- COMSOL Multiphysics® and
- either the Battery Design Module, Chemical Reaction Engineering Module, Fuel Cell & Electrolyzer Module, or Liquid & Gas Properties Module and
- either the Battery Design Module, CFD Module, Chemical Reaction Engineering Module, Corrosion Module, Electrochemistry Module, Electrodeposition Module, Fuel Cell & Electrolyzer Module, Heat Transfer Module, Porous Media Flow Module, or Subsurface Flow Module and
- either the Battery Design Module, CFD Module, Chemical Reaction Engineering Module, Corrosion Module, Electrochemistry Module, Electrodeposition Module, Fuel Cell & Electrolyzer Module, Microfluidics Module, Polymer Flow Module, Porous Media Flow Module, or Subsurface Flow Module
The combination of COMSOL® products required to model your application depends on several factors and may include boundary conditions, material properties, physics interfaces, and part libraries. Particular functionality may be common to several products. To determine the right combination of products for your modeling needs, review the Specification Chart and make use of a free evaluation license. The COMSOL Sales and Support teams are available for answering any questions you may have regarding this.