Numerical simulation of micro galvanic corrosion induced by intermetallic particle in Al alloys
Intermetallic particles (IMPs) in Al alloys play an important role in localized corrosion processes, and largely affect the service safety and reliability of the alloys. However, most of the experimental methods used so far only probe active corrosion sites on a projected two-dimensional surface, with no detailed information about how localized corrosion develops and how the local chemical environment changes inside the corroding volume, such as pits or crevices. Dynamic changes of the corroding surface remain to be unknown, and therefore it is difficult to predict propagation and consequences of the localized corrosion process.
In this work, by using the module of corrosion, Deformed Geometry (Tertiary Nernst-Planck) in COMSOL®, a FEM model considering the local electrochemical reactions on the electrode surface, the transport of O2 and ionic species (e.g., Al3+, H+, Cl-) and the homogeneous reactions in the electrolyte, the precipitation of reaction products (Al(OH)3) and its influence on the surface activity, as well as a dynamic moving dissolution surface was established. As a first step, an Al matrix with a micrometer-sized cathodic intermetallic particle exposed in 0.1M NaCl has been considered, and the heterogeneous microstructure of the alloy was defined by Matlab® programing. The simulation predicts the dynamic changes of the corroding surface, and the flow and distribution of ionic species and of O2 in space and time. Different with other modelling works, the blocking effect of precipitated corrosion product was quantitatively described by the surface coverage parameter, which was defined by the interface of Boundary ODEs and DAEs interface, and acts as a boundary condition on the electrode surface. This blocking effect leads to a decreasing surface activity and eventual termination of the micro-galvanic corrosion.
As further applications of the basic model, we investigated the effects of key geometric parameters by introducing a variable radius of cathodic particle (range 0.5 to 4 μm) and the width of the assumed anodic ring surrounding the particle (range 0.1 to 2 μm). Moreover, by introducing the chemical-dependent electrochemical kinetics as input parameters, the effects of chemical factors including pH (range 4 to 9) and O2 concentration of the bulk solution were also investigated. Simulation results basically are consistent with reported experimental scenarios. This work deepens our understanding about the investigated localized corrosion process by providing quantitative evidences for many of the empirical conclusions.
As an important part of our efforts to establish a comprehensive FEM model for simulation of micro-galvanic corrosion induced by intermetallic particles in Al alloys. We believe this work contributes significantly to the advancement in the field of corrosion science and technology.
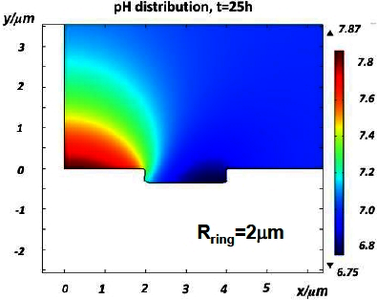
Download
- yin_poster.pdf - 1.86MB
- yin_abstract.pdf - 0.08MB