The Composite Materials Module utilizes specialized layered material technology and provides two theories that can be used to accurately model composite shells: layerwise theory and equivalent single layer theory. The layerwise theory is suitable for thick to moderately thin composite shells with a limited number of layers. The ESL theory is suitable for thin to moderately thick shells and can accommodate many layers without significant performance impact. It is also possible to combine these two theories to analyze the composite laminates. These theories can be used to optimize the layup and other parameters of a laminate by performing multiscale, multiphysics, and various failure analyses.
Composite Materials Module
Model Composite Structures for Improved Product Design
A composite material is a heterogeneous material composed of two or more integrated constituents for enhanced structural performance. The Composite Materials Module is an add-on to the Structural Mechanics Module that includes specialized modeling tools and functionality for analyzing layered composite structures. Layered composite materials, such as fiber-reinforced polymers, laminated plates, and sandwich panels, are widely used in the manufacturing of aircraft components, spacecraft components, wind turbine blades, automobile components, buildings, boat hulls, bicycles, and safety equipment.
Additionally, the Composite Materials Module can be combined with other modules in the COMSOL® product suite, which makes it possible to include, for example, heat transfer, electromagnetics, fluid flow, acoustics, and piezoelectric effects in composite material models.
Contact COMSOL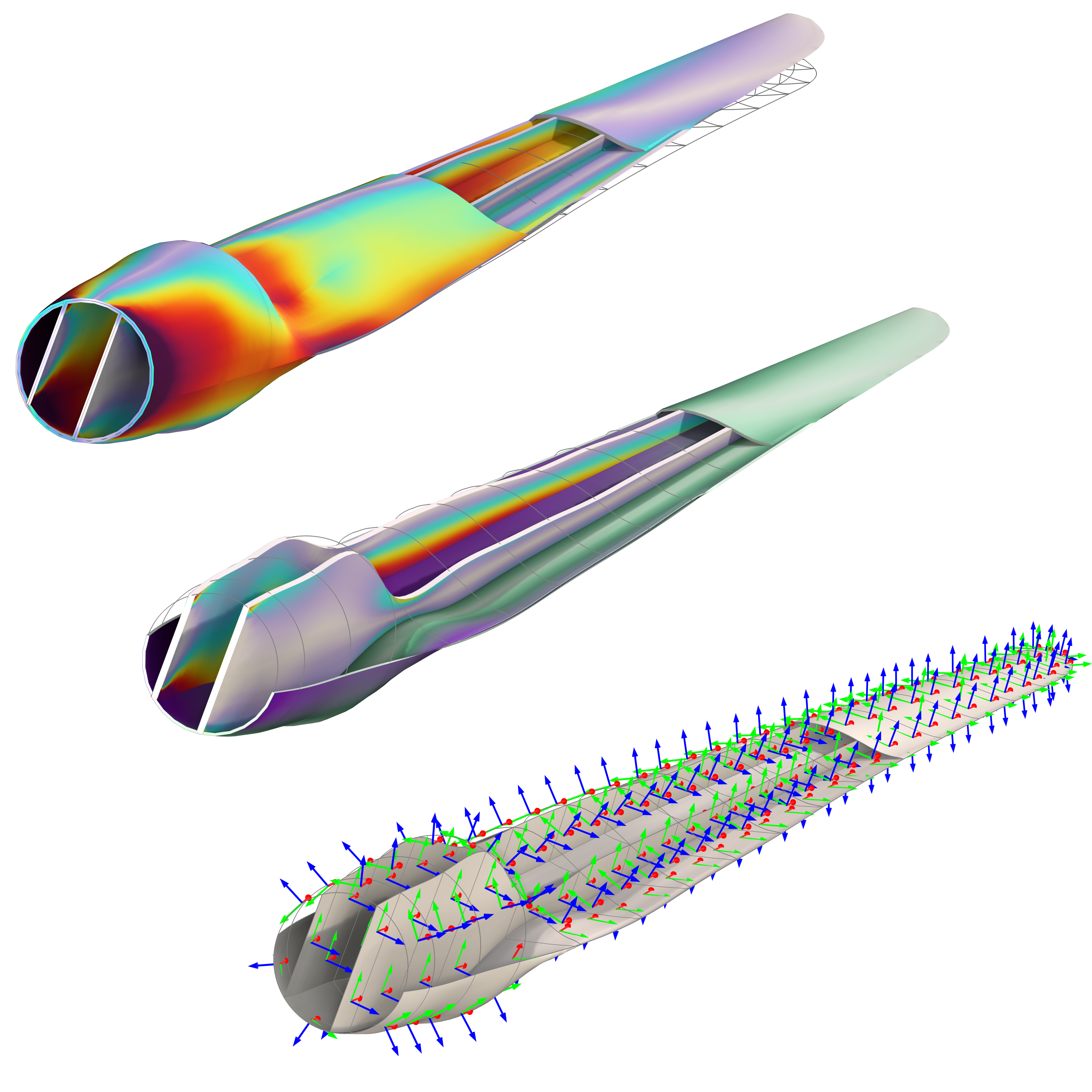
Laminate Theories to Define and Visualize Laminates
The analysis of laminated composite shells is commonly based on layerwise theory or equivalent single layer (ESL) theory.
What Can Be Modeled with the Composite Materials Module
Perform various structural analyses for composite laminates with the COMSOL® software.
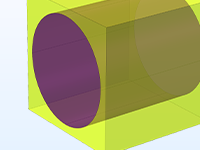
Micromechanics and Macromechanics
Compute homogenized material properties and macroscopic responses of composite laminates.
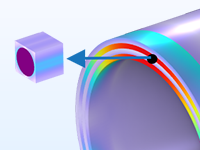
Multiscale Analysis
Evaluate the structural response of a composite structure at both the macroscale and microscale.
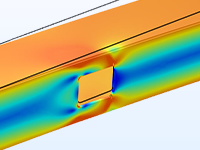
Nonlinear Materials1
Incorporate nonlinear material models in a layered composite.
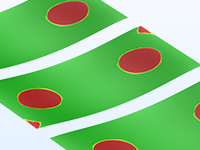
Delamination
Model delamination initiation and propagation in a composite laminate.
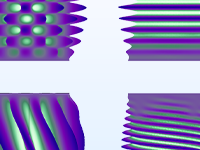
Linear Buckling
Compute critical load factors and mode shapes under compressive loading.
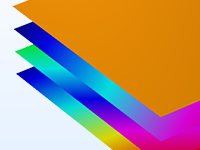
First-Ply Failure
Evaluate the structural integrity of a laminated composite shell.
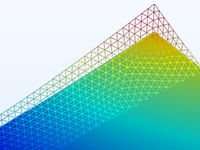
Composite Optimization2
Optimize composite layups, ply thicknesses, fiber orientations, and material properties.
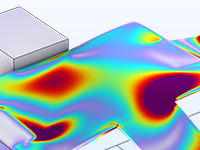
Structural Connections
Couple shell and layered shell elements with other structural elements using multiphysics couplings.
- Requires the Nonlinear Structural Materials Module
- Requires the Optimization Module
Specialized Tools for Defining and Visualizing Laminates
The Composite Materials Module offers a set of specialized tools for visualizing composite laminates that are made up of several layers.
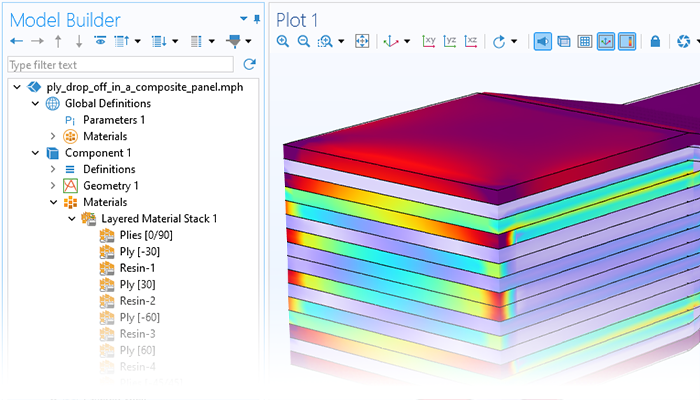
Layered Shell Interface
The Layered Shell interface, available in 3D, provides an approach based on layerwise theory for a detailed analysis of composite laminates. The materials in the individual layers can be nonlinear. It also supports different shape order for the displacement field in the reference surface and in the through-thickness direction. The Layered Shell interface includes full 3D stress and strain distribution results, enabling the computation of interlaminar stresses and the study of stress variations inside each lamina, for example.
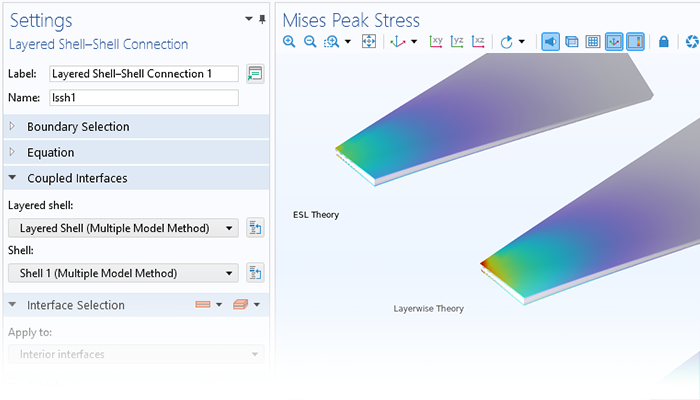
Multiple Model Method
The Layered Shell interface based on layerwise theory is accurate but computationally expensive. The Shell interface based on an equivalent single layer theory is computationally lean but unable to capture accurate through-thickness results. The multiple model method — which combines these two theories in the different parts of a composite laminate — is the best choice in terms of accuracy and performance for modeling sandwich composite structures.
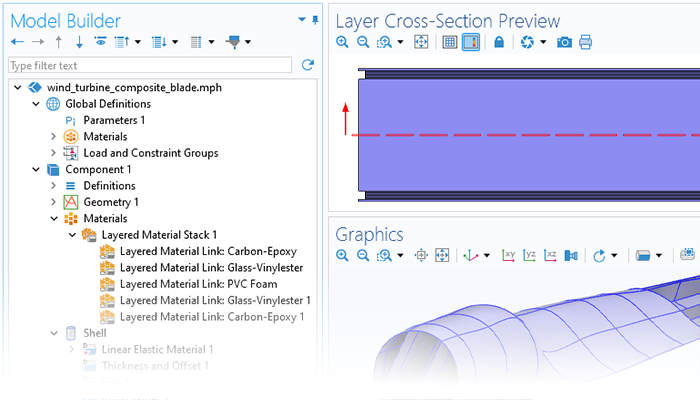
Layered Material Feature
The Layered Material node can be used to define a layup where each layer has its own material data, thickness, and principal orientation. There is also functionality for defining material properties for the interfaces between layers. Layered materials defined in this way can be combined using the Layered Material Link or Layered Material Stack node to create more complex layered materials, which is particularly convenient when the layup is repetitive, symmetric, or antisymmetric. These nodes include action buttons for visualizing the 2D or 3D preview plots of composite laminates.
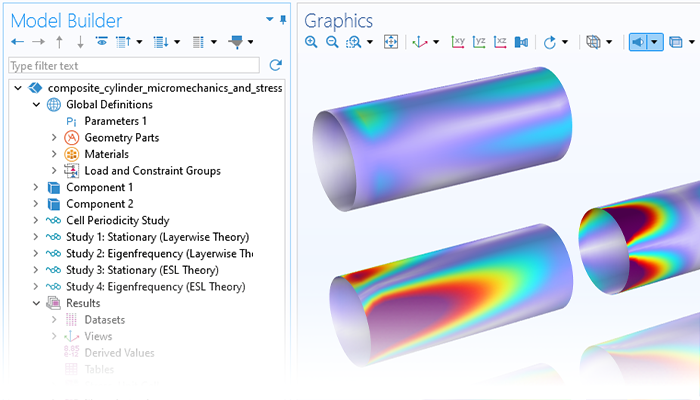
Layered Material Slice Plot
The Layered Material Slice plot provides more freedom in terms of creating slices in a composite laminate. This feature is useful in the following cases: when creating a slice only in one or a few selected layers, when creating a slice through some or all layers but not necessarily placing them in the through-thickness direction, and when examining a particular layer in detail and creating a slice at a position within the layer, away from the midplane.
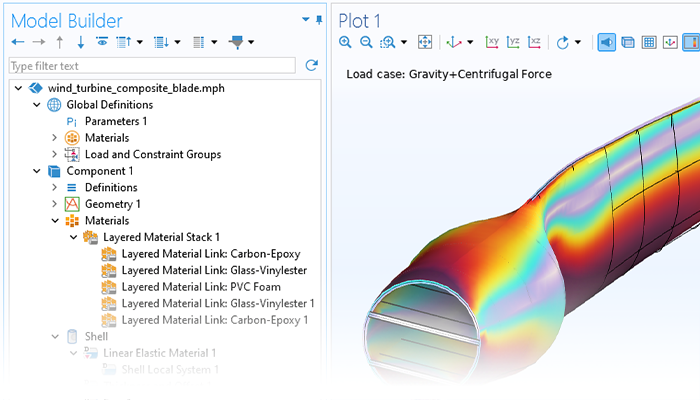
Shell Interface
The Shell interface is augmented with a material model, based on an equivalent single layer theory, that computes homogenized material properties of the entire laminate and solves only at midplane. Various inelastic effects like plasticity and viscoplasticity can be added to the individual layers of the laminate. The results include full 3D stress and strain distributions, so you can study stress variations inside each lamina, for example.
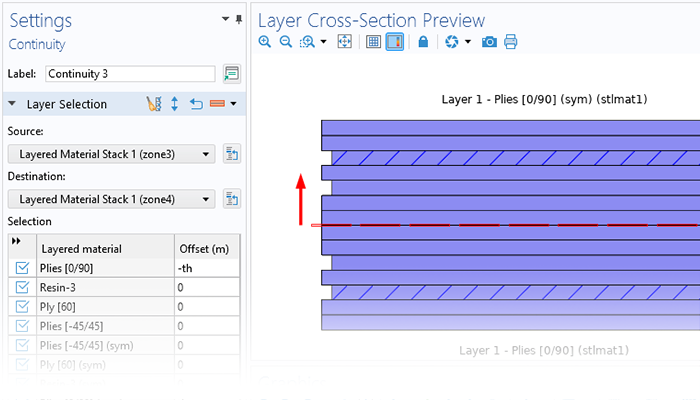
Layered Material Connection
When joining two different laminates in a side-by-side configuration or modeling a ply drop-off situation, it is possible to use the Layered Material Stack node together with the Continuity node in the Layered Shell interface. The connection area of the two laminates can be controlled through different options. The connected layers from both the laminates can be visualized using the Layer Cross Section Preview plot available in the Continuity node.
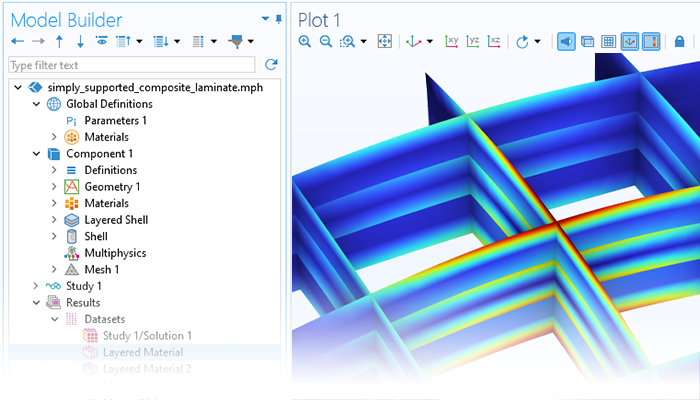
Layered Material Dataset
The Layered Material dataset is used to display the results of the simulation on a geometry that has a finite thickness. This dataset can be used to scale the laminate thickness in the normal direction, which is useful for visualizing thin laminates. The dataset offers the option to evaluate results at mesh nodes, interfaces, or layer midplanes, and it is also possible to select or deselect certain layers of a laminate.
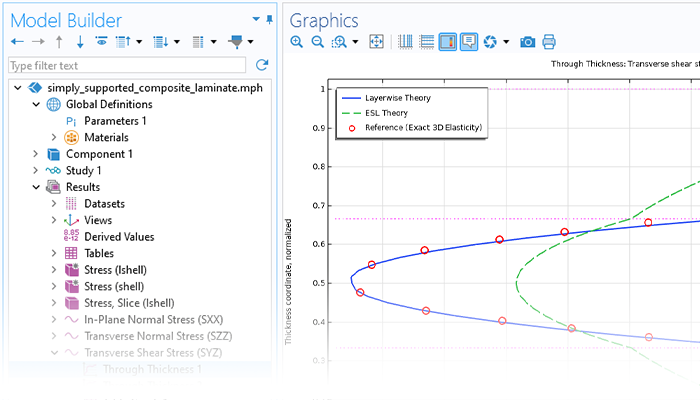
Through Thickness Plot
The Through Thickness plot makes it possible to visualize the variation of any quantity at a particular position on the boundary against the laminate thickness. One or more geometric points on the boundary can be selected, or cut point datasets can optionally be created. It is also possible to specify the point coordinates directly. Unlike other graphs, the result quantity is plotted on the x-axis, while the thickness coordinate is plotted on the y-axis.
Multiphysics Couplings for Extended Analyses
There are two fundamentally different types of interaction between the mechanics in a laminate and other processes. For physical processes that occur inside the laminate, all of the physical phenomena can be solved for simultaneously, including the couplings between them. In other physical processes, the laminate acts as a boundary for a 3D domain where something important occurs. The following multiphysics couplings are available with built-in couplings:
- Heat transfer1
- Electric currents2
- Piezoelectricity2
- Piezoresistivity2
- Poroelasticity3
- Acoustics–composite interaction4
- Fluid–composite interaction5
- Requires the Heat Transfer Module
- Requires the AC/DC Module or MEMS Module
- Requires the Porous Media Module
- Requires the Acoustics Module
- For turbulent flow, requires the CFD Module
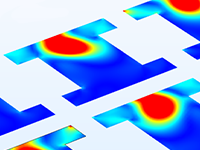
Heat Transfer and Electric Currents
Model Joule heating and thermal expansion inside a composite laminate with layered material technology.
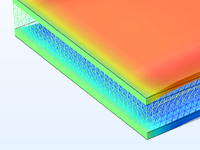
Piezoelectricity
Simulate piezoelectric composites used to create smart structures like sensors and actuators.
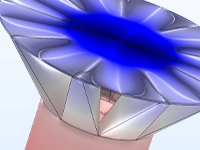
Acoustics–Composite Interaction
Model vibroacoustics by coupling the composite laminate with a surrounding acoustic domain.
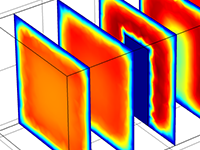
Fluid–Composite Interaction
Use the Shell and Layered Shell interfaces to model composite laminates interacting with fluid domains.
Every business and every simulation need is different.
In order to fully evaluate whether or not the COMSOL Multiphysics® software will meet your requirements, you need to contact us. By talking to one of our sales representatives, you will get personalized recommendations and fully documented examples to help you get the most out of your evaluation and guide you to choose the best license option to suit your needs.
Just click on the "Contact COMSOL" button, fill in your contact details and any specific comments or questions, and submit. You will receive a response from a sales representative within one business day.
Next Step
Request a Software Demonstration